2025 Szerző: Howard Calhoun | [email protected]. Utoljára módosítva: 2025-06-01 07:14
A késleltetett kokszoló egységek a nehézolaj-finomítás leggyakoribb hardvermegoldásai. Készülékük 2 fő modult tartalmaz - reaktort, ahol az alapanyag melegítése és kokszolása történik, valamint mechanikai feldolgozást. Az üzemek tervezése szakaszosan történik, és magában foglalja a technológiai berendezések számítását és kiválasztását, a műszaki és gazdasági mutatók meghatározását.
Úticél
A kokszolás technológiai folyamata az olajfinomítás egyik módja. Fő célja nagy darabos kőolajkoksz előállítása. Az iparban 3 kokszolási módot használnak:
- Időszakos, kockás. Az alapanyagot vízszintes berendezésbe töltjük, alatta tűztérrel felmelegítjük, majd 2-3 órán át kalcináljuk. Ezt követően a kemencét lehűtik, és a készterméket kirakodják. Ez a módszer a legegyszerűbb és legkevésbé produktív.
- Folyamatos. Ez a módszer még az ipari fejlődés szakaszában van.
- Félig folyamatos, jelenleg érkezetta legelterjedtebb.
Az ultrakésleltetett kokszolóegységek a technológiai berendezések legújabb típusai. Ezekben a nyersanyagot kemencében előmelegítik, majd fűtetlen reakciókamrákba töltik, amelyek hőszigetelő réteggel rendelkeznek a szükséges hőmérséklet fenntartása érdekében. A reaktorok száma és mérete, a kemencék teljesítménye befolyásolja az egész erőmű teljesítményét.
Az első oroszországi DCU működését 1965-ben kezdték meg Ufaneftekhimben. Az üzem késleltetett kokszolója ma is működik. Termelékenysége a 2007-es rekonstrukció után a feldolgozott alapanyag tömegére vonatkoztatva mintegy 700-750 ezer tonna/év.
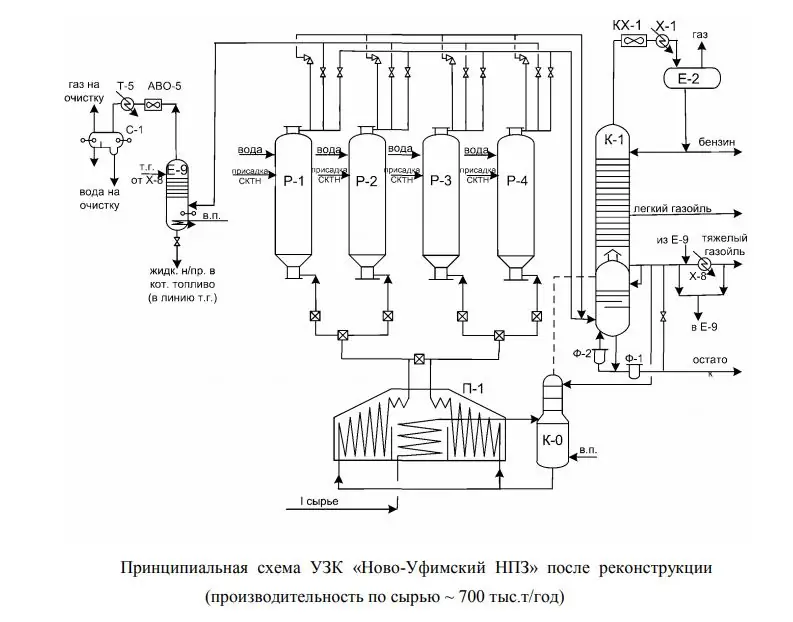
Végső termékek
A következő anyagokat nyerték ultrahangos vizsgálat során, kivéve a kokszot:
- kokszos gázok (üzemanyagként használják vagy propán-bután frakció előállítására dolgozzák fel);
- benzin;
- kokszpárlatok (üzemanyag, krakkolási alapanyag).
A hazai ultrahangos vizsgálógépeken a kokszhozam 20-30 tömegszázalék. Ez a mutató elsősorban a nyersanyagok minőségétől függ. A kohászati iparban van a legnagyobb igény erre a termékre (anódok és elektródák, alumínium, csiszolóanyagok, karbidok, szén-grafit anyagok, vasötvözetek gyártása). Az első Ufa DCU mellett további késleltetett kokszoló egységek is épültek Oroszországban: az Omszki Finomítóban, Novokuibisevszki Finomítóban, LLC LUKOIL-Volgogradneftepererabotka, LUKOIL-Permnefteorgsintez, LUKOIL-Permnefteorgsintez, az Angarsk Petrolkémiai Vállalatnál, NOVOIL OJSC (Ufa), TANECO PJSC (Nizsnekamsk).
Alapanyagok
A kokszoláshoz használt élelmiszer-anyagok 2 csoportra oszthatók: elsődleges és másodlagos feldolgozás termékei. A késleltetett kokszolóegységekben a következő anyagokat használják nyersanyagként:
- fűtőolaj;
- félkátrány;
- tar;
- szénkátrány szurok;
- aszf alt és egyéb ipari olajtermékek;
- folyékony szénmaradék;
- nehéz pirolízis és palakátrány;
- termikus repedés maradványai;
- ásványolaj-bitumen és nehézolajok.
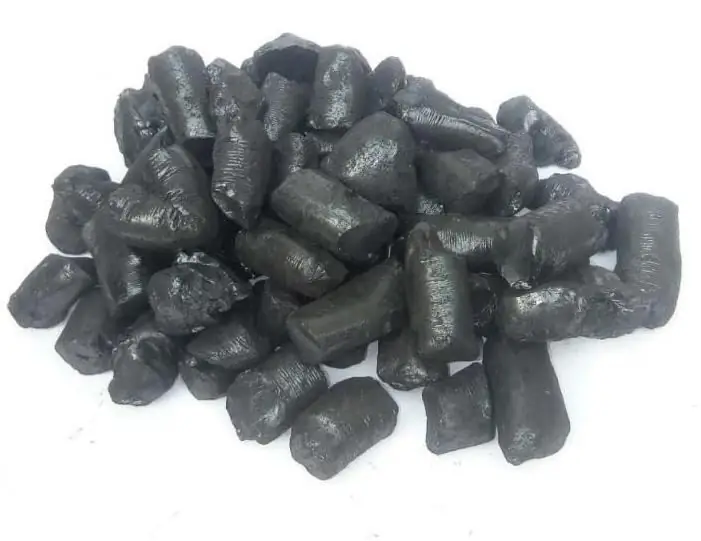
Az erősen aromatizált olajmaradványok jelenleg a leggyakoribb alapanyagok.
Befolyásolás a technológiai paraméterekre
A kokszoló üzem alábbi paraméterei a takarmány-alapanyagok tulajdonságaitól függenek:
- a reakciókamra hatékonysága;
- beérkezett termékek minősége;
- kokszleadó;
- a folyamat feltételei.
A legfontosabb alapanyag-paraméterek:
- Kokszozás, az aszf alt-gyantaszerű anyagok tartalmától függően. A kokszosodási érték 10-20% tartományban legyen. Kisebb értéknél a kokszhozam csökken, nagyobbnál pedig lerakódások halmozódnak fel a kemencék tekercseiben. A kokszolóképességet a tégelyben lévő szilárd maradék tömege határozza meg, miután az olajtermékmintát melegítettük.
- Sűrűség.
- Kémiai összetétel. Tól tőlkáros szennyeződések, amelyek a legnagyobb hatással vannak a koksz minőségére, ként bocsátanak ki (nem lehet több, mint 1,5 tömegszázalék). Attól függően, hogy a koksz technológiai folyamatban milyen célt szolgál, célszerű különböző típusú nyersanyagokat használni. Tehát a végtermék rostos szerkezetének eléréséhez paraffin alapú anyagokat használnak.
A kokszhozam arányos a takarmánysűrűséggel és az aszf alténtartalommal.
Kokszolási szakaszok
A késleltetett kokszoló egységek technológiai folyamata hosszú és folyamatos, az alapanyag beszállítástól a késztermék kirakodásáig. Hagyományosan 3 szakaszra oszlik:
- Bomlási reakciók, desztillátumfrakciók képződése, intermedierek, kondenzáció.
- A gázok telítetlen szénhidrogén-tartalmának jelentős csökkenése, a maradékkomponensek molekulatömegének növekedése, ciklizációs reakciók.
- A maradék aszf altének tartalmának akár 26%-os növelése, a gyanták és olajok mennyiségének csökkenése. A folyékony maradékot szilárd kokszlá alakítsa.
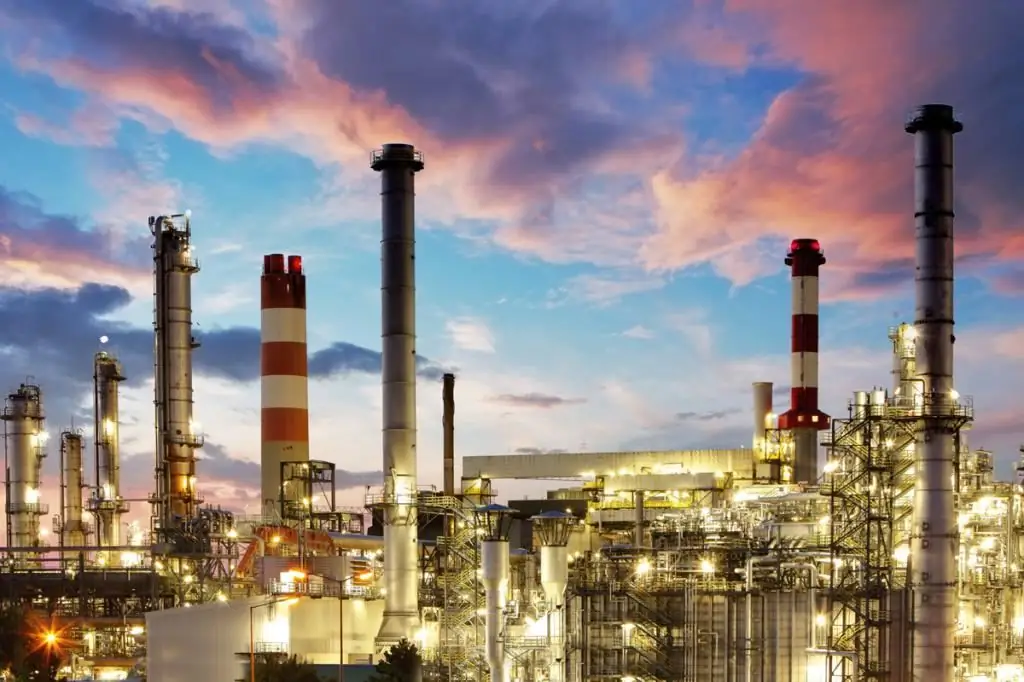
Osztályozás
A késleltetett kokszolóegységeknek 2 fő típusa van elrendezésük szerint: egyblokkos és duplablokkos.
A kétblokkos üzemek között 4 típus létezik, melyeket a következő tervezési és technológiai jellemzők jellemeznek:
- Kokszolókamrák belső átmérője - 4,6 m Sátorfűtő kemencék, négy párban működő kamra. A kokszolás során nyert kerozint és gázolajat melegítésre használják.
- Kóklakamrák Ø 5,5 m Nyersanyag - közvetlen lepárlású fűtőolajok erősen aromás szénhidrogének bevezetésével, amelyek növelik a minőségi termék hozamát.
- Ötvözött acélból készült reaktorok Ø 5,5 m, magasság 27,6 m, cső alakú kemencék térfogati fektető égővel, megnövelt keresztmetszetű felső szelepek, radioaktív szintmérők, amelyek lehetővé teszik a koksz-hab fázisleválasztás helyének regisztrálását. A legújabb innováció segít a reaktor hasznos térfogatának jobb kihasználásában. Turbulátorok ellátása mosószer adalékokkal a tekercsek kokszosodásának csökkentésére, hűtött gázolaj a fejcsövekben.
- Reakciókamrák Ø 7 m, magasság 29,3 m Nyersanyag tengelyirányú bevitel a reaktorokba, távirányítós kokszleeresztő hidraulikus rendszer, elektromos daruk, raktárak padló típusú tárolóval.
Alkalmazott berendezések
Az ilyen típusú berendezésekkel felszerelt berendezések a céltól függően a következő csoportokba sorolhatók:
- Technológiai, közvetlenül részt vesz a kokszolási folyamatban (kemencék, oszlopberendezések, hőcserélők, reaktorkamrák, kockák, hűtőszekrények, szivattyúk, csővezetékek, műszerek, csapok és egyéb elzáró- és kapcsolószelepek).
- Szennyvíz - a víz összegyűjtése és kezelése a munkaciklusba való visszatéréshez (hűtési és kokszkinyerési műveletek).
- Berendezés a koksz kamrákból történő kiürítésére (kockák). A modern gépesített beépítéseknél lehet mechanikus és hidraulikus (hevederek, csörlők, fésűk, vágók, rudak, tornyok, gumihüvelyek).
- A késztermék szállítására és feldolgozására szolgáló eszközök (befogadó csúszdák és rámpák, daruk, szállítószalagok, adagolók, zúzógépek, raktárak).
- Gépek és berendezések a munka gépesítéséhez.
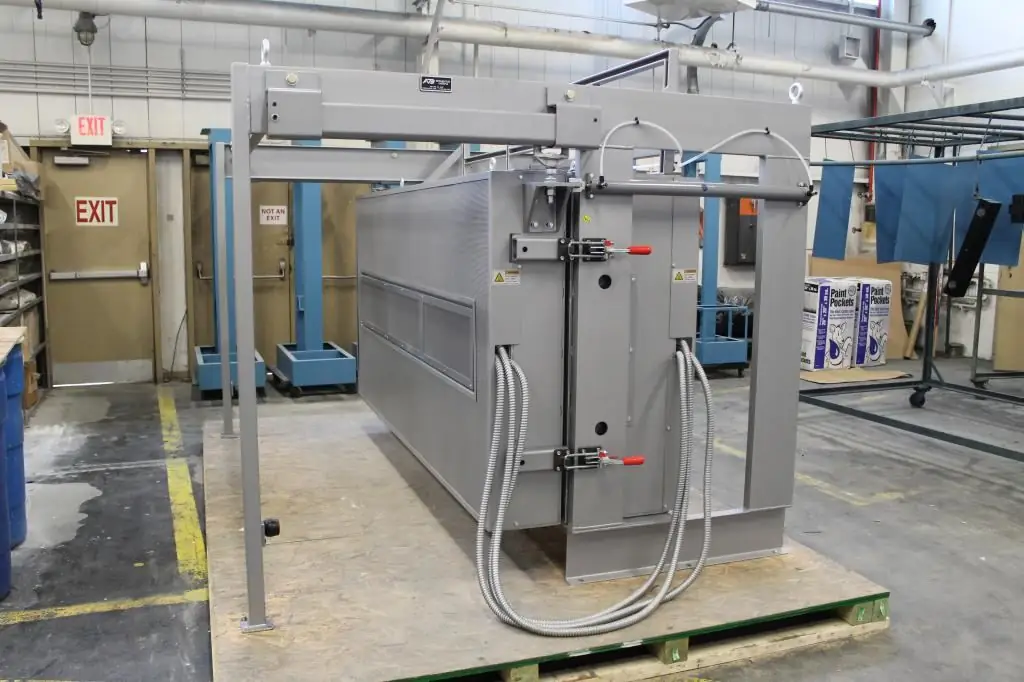
A késleltetett kokszoló üzemek tervezésekor alaposan át kell gondolni a reakciókamrák és kemencék kialakítását, mivel a munkaciklus időtartama működésük megbízhatóságától függ.
Folyamatparaméterek
A kokszolási technológia fő paraméterei:
- Recirkulációs arány, a kemencék reakciótekercseinek teljes terhelésének és a teljes üzem terhelésének aránya a nyersanyagok tekintetében. Értékének növekedésével a jó minőségű koksz, gáz és benzin hozama nő, a nehézgázolaj mennyisége viszont csökken.
- Nyomás a reakciókamrában. Ennek csökkenése a gázolaj hozamának növekedéséhez, a koksz és gáz hozamának csökkenéséhez, valamint a habzás növekedéséhez vezet.
- Folyamat hőmérséklet. Minél nagyobb, annál jobb a koksz minősége az illékony anyagok mennyisége, szilárdsága és sűrűsége szempontjából. A maximális értéket korlátozza a kemence és a csővezetékek kokszosodásának veszélye, ami csökkenti a tekercsek tartósságát. Minden nyersanyagtípusnak megvan a maga optimális hőmérséklete.
A késleltetett kokszoló egységek építése magas tőkeköltséggel jár. Ezért leggyakrabban egy már működő berendezés-komplexum rekonstrukcióját végzik. Ezt a ciklus csökkentésével érik elkokszolás, új reakciókamrák bevezetése vagy a recirkulációs arány csökkentése.
Működési elv
A késleltetett kokszoló egységek egy vagy több páros kamracsoportból állnak, amelyekben az egyik kamra a kokszgyártás szakaszában, a másik pedig a kirakodáskor vagy közbenső állapotban működik. A kiindulási anyag bomlási folyamata csőkemencében kezdődik, ahol 470-510 °C-ra melegítik fel. Ezt követően a nyersanyag fűtetlen kamrákba kerül, ahol a vele együtt járó hő hatására mélyen kokszosodik.
A gáz-halmazállapotú és folyékony szénhidrogéneket frakcionált elválasztás céljából egy desztillációs oszlopba engedik ki. A koksz a gépi feldolgozó részlegbe kerül, ahol kirakodják, szétválogatják és elszállítják. A késztermék rétegébe kutat fúrnak, és egy hidraulikus vágót helyeznek el. Fúvókái 20 MPa nyomásig működnek. Az elválasztott kokszdarabok egy vízelvezető platformra esnek, ahol a vizet leeresztik. A terméket ezután kisebb darabokra aprítják és frakciókra osztják. Ezután a koksz a raktárba kerül.
Az ultrahang elvi diagramja az alábbi ábrán látható.
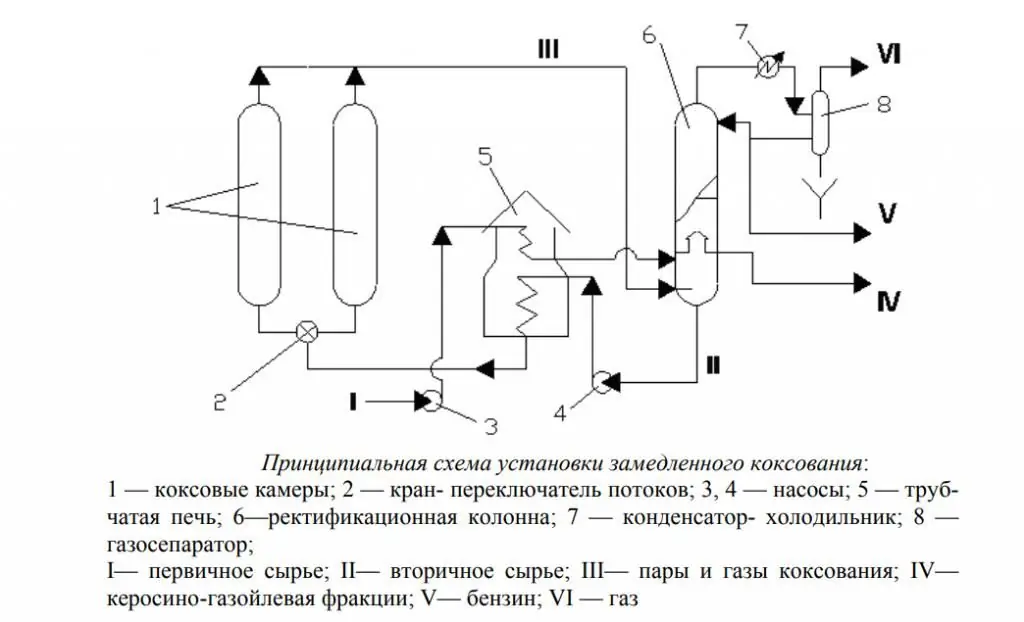
Kokszkamrák
A kamrák egy reaktor, amely a teljes telepítés alapja. A kamra működési ciklusa általában 48 óra, azonban az elmúlt években 18 és 36 órás üzemmódban működő ultrahangos készülékeket terveztek.
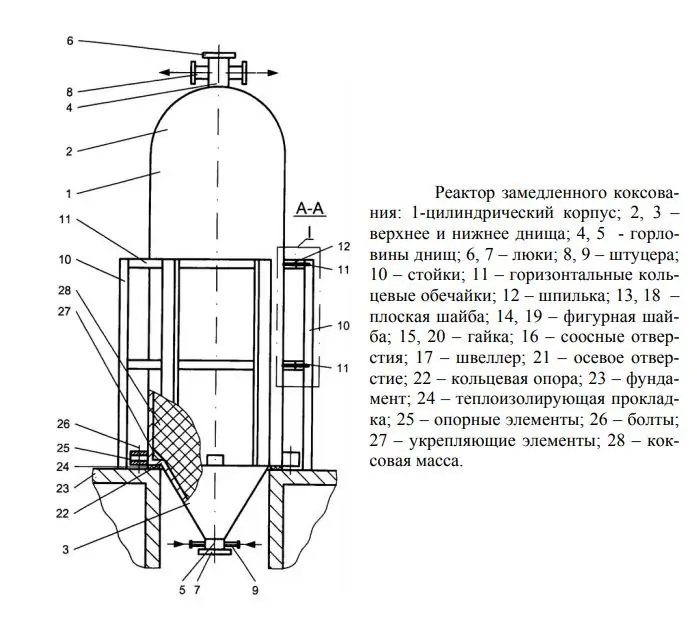
Egy reaktor működési ciklusa a következő műveletekből áll:
- alapanyag berakodás, kokszolási folyamat (1 nap);
- off (1/2 óra);
- hidrotermikus kezelés (2,5 óra);
- a termék vízhűtése, víz eltávolítása (4 óra);
- termék kirakása (5 óra);
- aknák tömítése, nyomáspróba forró gőzzel (2 óra);
- fűtés olajgőzökkel, átkapcsolás üzemi ciklusra (3 óra).
Dizájn
A késleltetett kokszolóegység projekt fejlesztése a következő sorrendben történik:
- a szükséges termelékenység meghatározása, t/év;
- erőforrásbázis elemzés;
- a kokszolási folyamat elméleti anyagmérlegének elkészítése különféle típusú nyersanyagokhoz;
- a fő anyagáramlások meghatározása;
- telepítési koncepció kidolgozása;
- a reaktorok méretének és számának indoklása;
- egy kamra koksztöltési idejének meghatározása és hidraulikai számítása, a reaktor működési ütemtervének elkészítése;
- a kamra hőmérsékleti terhelésének kiszámítása;
- konvekciós és sugárzási kamrák számítása;
- gyártósor-elrendezés fejlesztése;
- egyéb fő berendezések technológiai számításai (desztillációs oszlop, kemencék, hűtőszekrények stb.);
- felügyeleti és vezérlőrendszer fejlesztése, automatizálási eszközök kiválasztása;
- vészhelyzeti védelmi rendszerek leírása;
- környezetvédelmi szempontok és biztonsági intézkedések fejlesztése;
- gazdasági mutatók meghatározása (tőkeköltség, kiszolgáló személyzet létszáma, bérszámfejtés,nyersanyagok és segédanyagok előállítási költségei, éves gazdasági hatás, termékköltség).
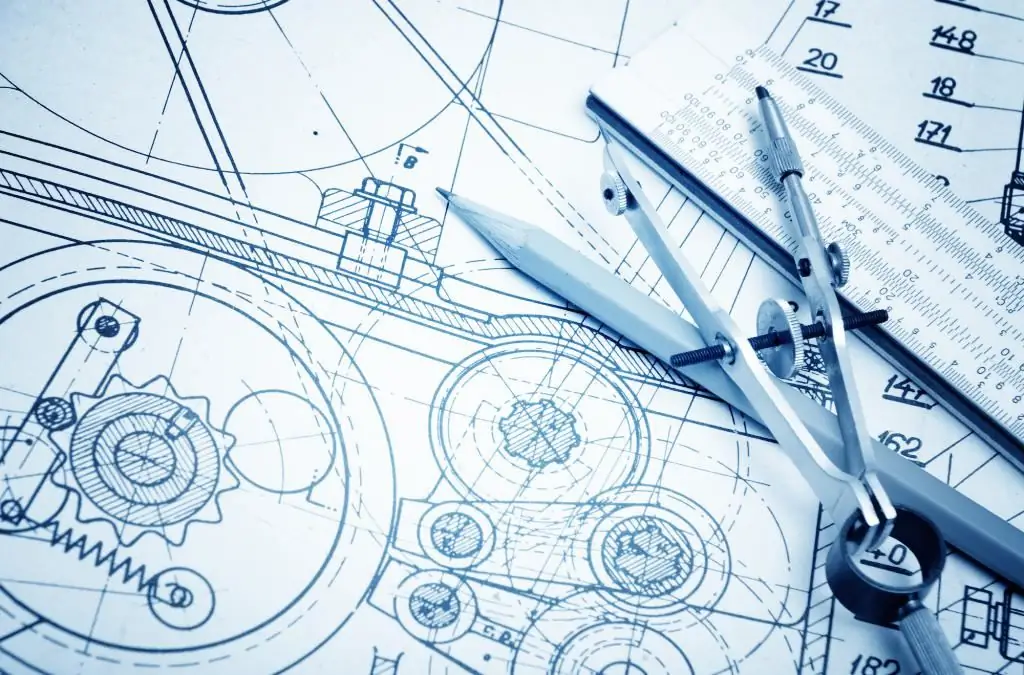
A késleltetett kokszoló egység éves kapacitásának kiszámítása a következő képlet szerint történik:
N=P x t, ahol P az üzem kapacitása, t/nap;
t az egy év munkanapjainak száma.
A termék fizikai kibocsátása az alap- és a tervezési lehetőségek szerint a telepítés anyagmérlegétől függ.
Ajánlott:
Elektromos mozdony 2ES6: létrehozás története, leírás fotóval, főbb jellemzők, működési elv, működési és javítási jellemzők
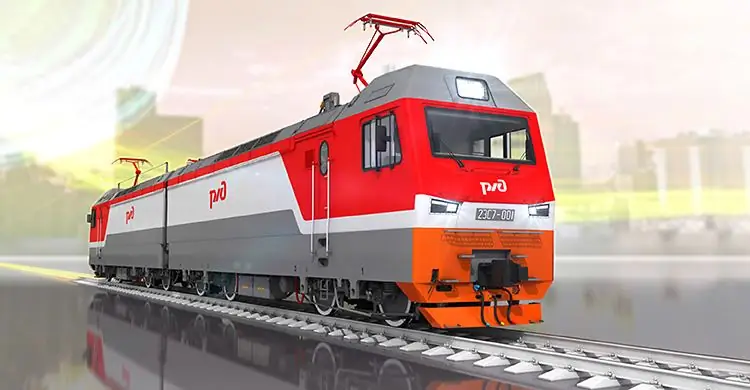
Ma a különböző városok közötti kommunikáció, személyszállítás, áruszállítás sokféleképpen zajlik. Az egyik ilyen út a vasút volt. A 2ES6 elektromos mozdony a jelenleg aktívan használt közlekedési módok egyike
Gyémánt fúrógép: típusok, készülék, működési elv és működési feltételek
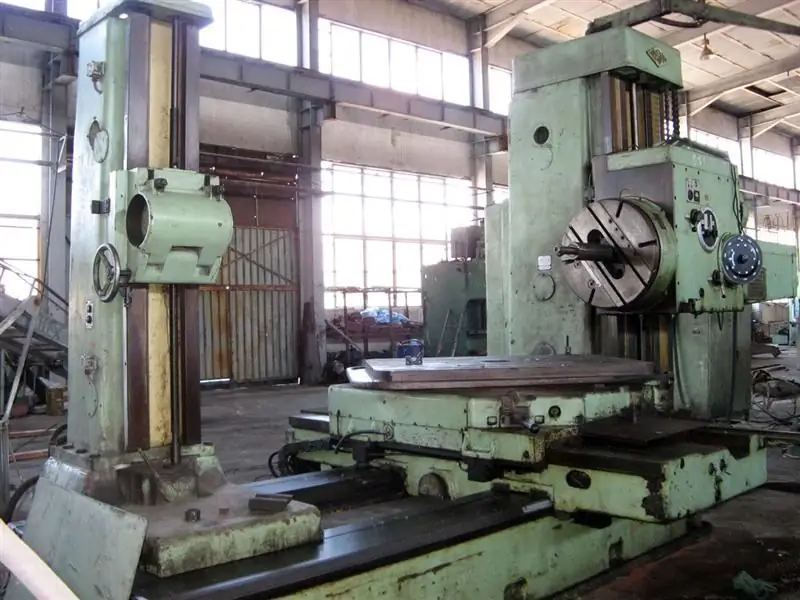
A bonyolult forgácsolási irány-konfiguráció és a szilárdtest-megmunkáló berendezések kombinációja lehetővé teszi a gyémántfúró berendezések számára, hogy rendkívül kényes és kritikus fémmegmunkálási műveleteket hajtsanak végre. Az ilyen egységekre bízzák a formázott felületek kialakítását, a furatkorrekciót, a végek kidolgozását stb. A gyémánt fúrógép ugyanakkor univerzális az alkalmazási lehetőségeket tekintve különböző területeken. Nemcsak speciális iparágakban használják, hanem magánműhelyekben is
Késleltetett fizetés "Tele2": kényelmes módja a kapcsolattartásnak
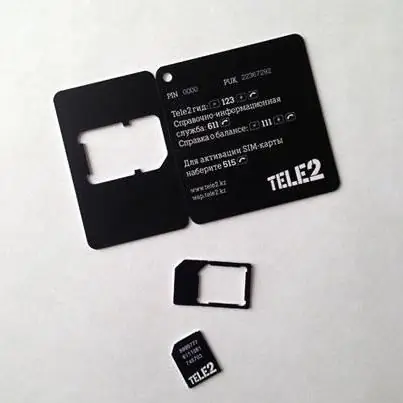
Ismerős helyzet – fel kell vennie a kapcsolatot egy barátjával, de a telefonban kifogyott a pénz. Mit kell tenni? Manapság számos módja van számlájának finanszírozásának. Tegyen egy sétát a legközelebbi terminálhoz, utaljon át pénzt kártyájáról vagy aktiválja az automatikus fizetést, és felejtse el a kommunikációs problémákat. De ha a pénzügyek átmenetileg románcokat énekelnek, akkor a halasztott fizetés segít. A Tele2 kínálja a leghűségesebb csatlakozási feltételeket, ezért érdemes alaposan szemügyre venni ezt a lehetőséget
Kis nyomású fűtőberendezések: meghatározás, működési elv, műszaki jellemzők, osztályozás, kialakítás, működési jellemzők, ipari alkalmazás
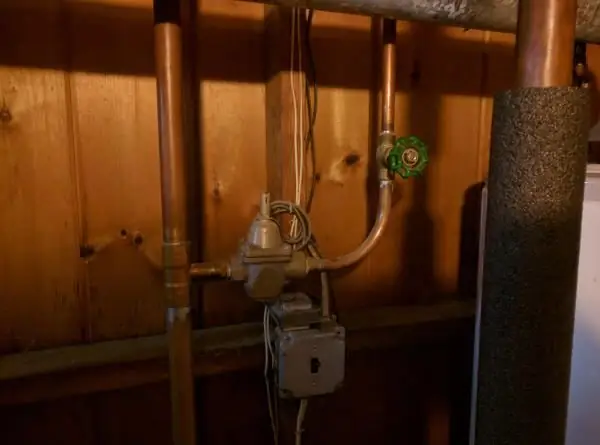
Az alacsony nyomású fűtőberendezéseket (LPH) jelenleg meglehetősen aktívan használják. Két fő típust gyártanak különböző összeszerelő üzemek. Természetesen teljesítményükben is különböznek egymástól
Kokszoló akkumulátorok: készülék, működési elv, cél. Kokszgyártás technológia
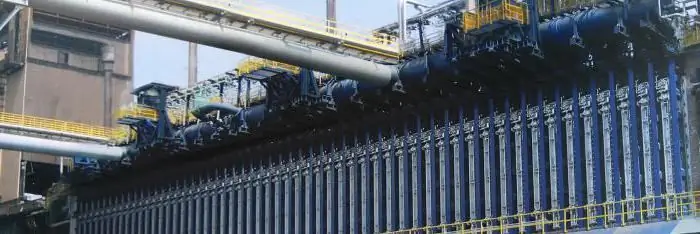
A kokszolókemencék akkumulátorai összetett és fontos ipari létesítmények. Munkájáról és eszközéről a cikkben fogunk beszélni