2025 Szerző: Howard Calhoun | [email protected]. Utoljára módosítva: 2025-06-01 07:14
A fémfeldolgozó ipar a fejlődés ezen szakaszában képes megoldani a különböző keménységű munkadarabok forgácsolásának és fúrásának összetett feladatait. Ez az anyag alapvetően új befolyásolási módjainak, köztük az elektromechanikai módszerek széles csoportjának kidolgozásával vált lehetővé. Az egyik leghatékonyabb ilyen technológia az ultrahangos feldolgozás (UZO), amely az elektroakusztikus sugárzás elvein alapul.
A dimenziós RCD alapelvei
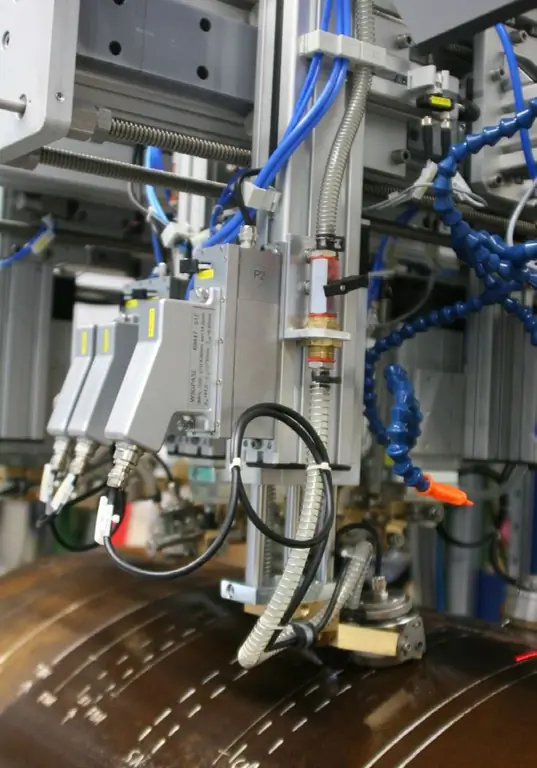
Dimenziós feldolgozás során a szokásos mechanikus marók és csiszolószerek közvetlen befolyásoló eszközként működnek. A fő különbség ebben a módszerben a szerszámot tápláló energiaforrásban rejlik. Ebben a minőségben az ultrahangos áramgenerátor 16-30 kHz-es frekvencián működik. Provokálugyanazon csiszolószemcsék oszcillációi ultrahang frekvencián, ami biztosítja a feldolgozás jellegzetes minőségét. Ezenkívül meg kell jegyezni a mechanikai hatások sokféleségét. Ez nem csak a szokásos vágó- és csiszolóelemek, hanem a szerkezet deformációja is a térfogatának megőrzése mellett. Sőt, az ultrahangos méretezés biztosítja, hogy a munkadarab részecskéi a minimálisra csökkenjenek még vágás közben is. Az anyagot befolyásoló szemcsék olyan mikrorészecskéket tarkítottak, amelyek nem befolyásolják a termék kialakítását. Valójában a szerkezet mintavételezéssel nem roncsolódik, azonban előfordulhat, hogy a repedések ellenőrizetlenül továbbterjednek.
Különbségek a plazmatechnológiától
A feldolgozás minőségét tekintve az ultrahangos és plazma módszerek sok hasonló tulajdonsággal rendelkeznek, amelyek nagy pontosságú vágás lehetőségét biztosítják. De a munkaelvben is jelentős különbség van köztük. Tehát, ha az UZO intenzív hatást gyakorol a csiszolóporra a vágószerszám oldaláról egy elektromos hullámgenerátor energiatámogatásával, akkor a plazmafeldolgozási módszer ionokkal és elektronokkal töltött ionizált gázt használ munkaközegként. Vagyis az ultrahangos és plazmafeldolgozás technológiái egyformán igénylik egy kellően erős energiagenerátor támogatását. Az első esetben ez egy ultrahangos elektromos berendezés, a második esetben pedig magas hőmérsékletű gáz- vagy izoterm berendezés, amely képes a munkaközeg hőmérsékleti rendszerét 16 000 °C-ra emelni. A plazmakezelés fontos eleme az elektródák és a plazma használataolyan anyagok, amelyek nagy teljesítményt biztosítanak a vágó irányított ívében.
Ultrahangos kezelőgépek
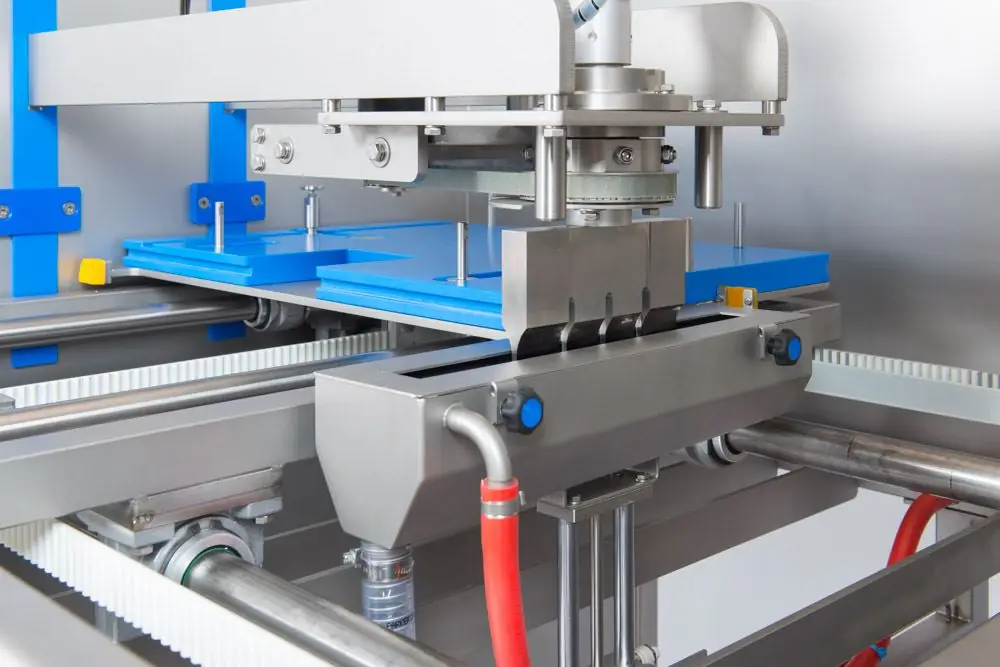
Most érdemes részletesebben foglalkozni az RCD megvalósításához használt berendezésekkel. A nagy iparágakban ilyen célokra gépeket használnak, amelyek generátorkészlettel vannak ellátva ultrahangfrekvenciás váltakozó áram előállítására. A generált áramot a mágneses átalakító tekercsére irányítják, amely viszont elektromágneses teret hoz létre a berendezés munkateste számára. Az ultrahangos feldolgozás azzal kezdődik, hogy a gép lyukasztója elektromágneses térben vibrálni kezd. Ennek a rezgésnek a frekvenciáját a generátor állítja be az adott esetben szükséges beállított paraméterek alapján.
A lyukasztó magnetosztriktív anyagból (vas, nikkel és kob alt ötvözetéből) készült, amely lineáris méretei változhatnak egy mágneses jelátalakító hatására. A végső kritikus szakaszban pedig a lyukasztó a hullámvezető-kondenzátor mentén vezérelt rezgések révén hat a csiszolóporra. Ezenkívül a feldolgozás mértéke és teljesítménye eltérő lehet. A szóban forgó berendezéseken ipari fémmegmunkálás történik masszív szerkezetek kialakításával, de vannak hasonló működési elvű kompakt készülékek is, amelyeken nagy pontosságú gravírozást végeznek.
Dimenziós RCD technika
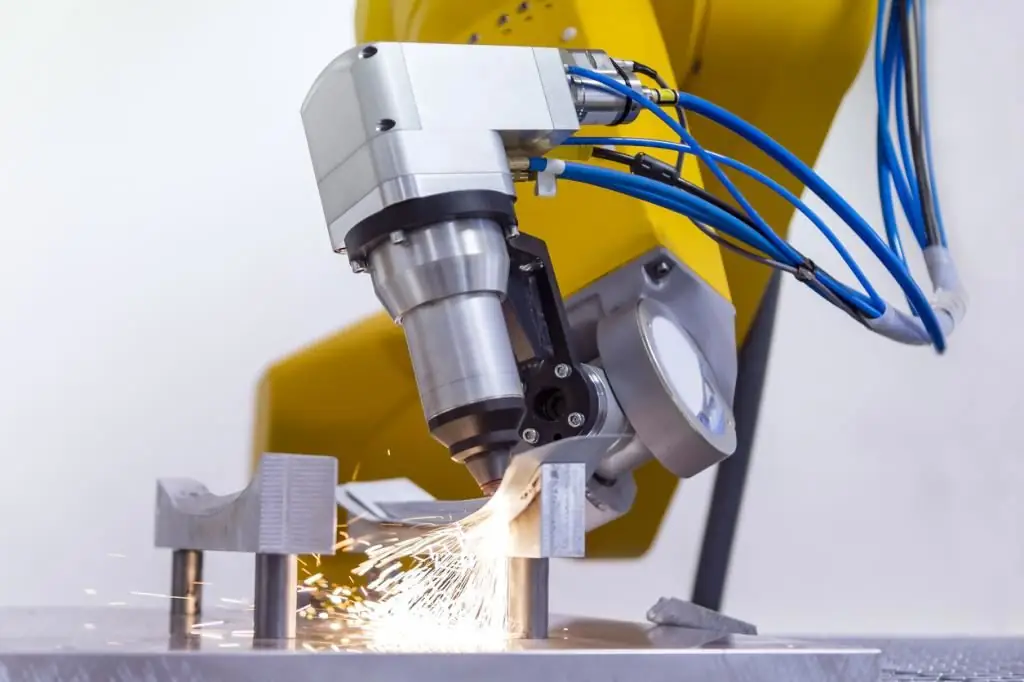
A berendezés telepítése és előkészítése utána célanyagból a csiszolószuszpenziót a műveleti területre - vagyis a termék felülete és az oszcilláló vég közötti térbe - juttatják. A szilícium- vagy bór-karbidokat egyébként általában magának csiszolóanyagnak használják. Az automatizált vonalakban vizet használnak porszállításra és hűtésre. A fémek közvetlen ultrahangos feldolgozása két műveletből áll:
- A koptató részecskék behatolása a munkadarab tervezett felületébe, melynek eredményeként mikrorepedések hálózata képződik, és a termék mikroszemcséi kilyukadnak.
- A csiszolóanyag keringése a feldolgozási zónában - a használt szemcséket új részecskék áramlása váltja fel.
Az egész folyamat eredményességének fontos feltétele, hogy mindkét eljárásban magas tempót tartsunk fenn a ciklus végéig. Ellenkező esetben a feldolgozási paraméterek megváltoznak, és a csiszolási irány pontossága csökken.
Folyamatjellemzők
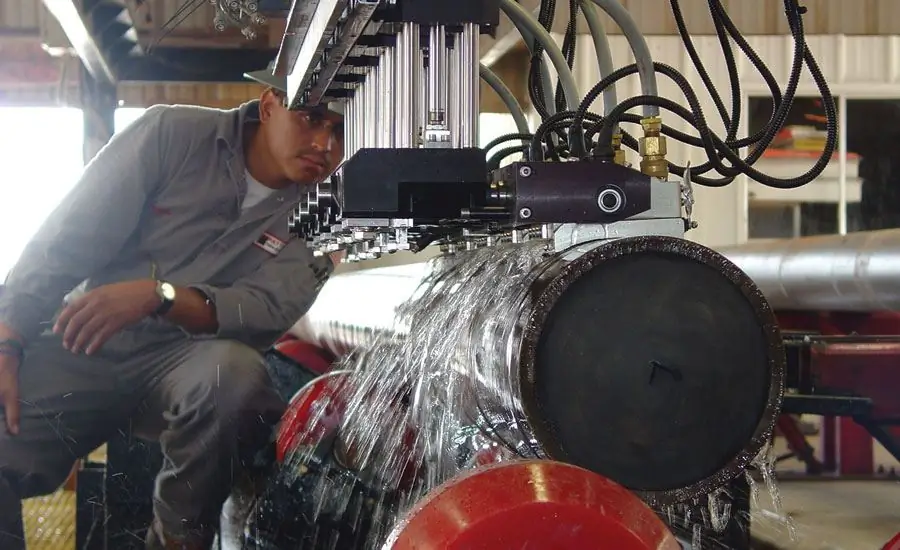
Az adott feladathoz optimális feldolgozási paraméterek előre be vannak állítva. Mind a mechanikai hatás konfigurációját, mind a munkadarab anyagának tulajdonságait figyelembe veszik. Az ultrahangos kezelés átlagos jellemzőit a következőképpen ábrázolhatjuk:
- Az áramgenerátor frekvenciatartománya 16-30 kHz.
- A lyukasztó vagy munkaeszközének lengési amplitúdója - az alsó spektrum a művelet elején 2-10 mikron, a felső szint pedig elérheti a 60 mikront.
- A csiszolóiszap telítettsége - 20-100 ezer.szemek 1 cm-es kockánként.
- A csiszolóelemek átmérője - 50-200 mikron.
Ezeknek a paramétereknek a változtatása nemcsak egyedi, nagy pontosságú lineáris feldolgozást tesz lehetővé, hanem összetett hornyok és kivágások pontos kialakítását is. Az összetett geometriákkal való munka sok szempontból lehetővé vált a lyukasztók jellemzőinek tökéletessége miatt, ami befolyásolhatja a csiszolóanyag összetételét a vékony felépítményű különböző modelleknél.
sorjátlanítás RCD-vel
Ez a művelet az akusztikus tér kavitációjának és eróziós aktivitásának növekedésén alapul, amikor 1 mikronos ultra-kis részecskéket juttatnak a csiszolóáramba. Ez a méret összevethető a lökéshanghullám hatássugárával, ami lehetővé teszi a gyenge sorjaterületek elpusztítását. A munkafolyamatot speciális folyékony közegben, glicerin keverékkel szervezzük. Tartályként speciális berendezést is használnak - fitomixert, amelynek pohárjában lemért csiszolóanyagok és munkarész található. Amint akusztikus hullámot alkalmaznak a munkaközegre, megkezdődik a koptató részecskék véletlenszerű mozgása, amelyek a munkadarab felületén hatnak. A szilícium-karbid és az elektrokorund finom szemcséi víz és glicerin keverékében hatékony sorjázást biztosítanak 0,1 mm-es méretig. Az ultrahangos kezelés tehát a hagyományos mechanikai csiszolás után is megmaradt mikrohibák pontos és nagy pontosságú eltávolítását biztosítja. Ha nagy sorjakról beszélünk, akkor érdemes növelni a folyamat intenzitását vegyi elemek hozzáadásával a tartályhoz.mint a kék vitriol.
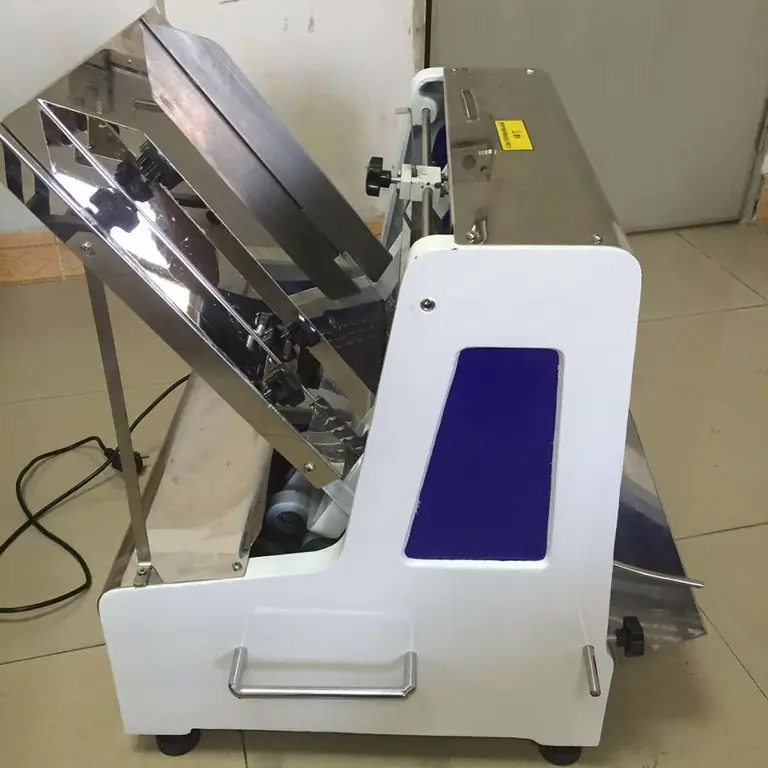
Alkatrészek tisztítása RCD-vel
A megmunkáló fémdarabok felületén különféle bevonatok és szennyeződések lehetnek, amelyeket valamilyen okból kifolyólag nem szabad eltávolítani hagyományos koptató tisztítással. Ebben az esetben a folyékony közegben végzett kavitációs ultrahangos feldolgozás technológiáját is alkalmazzák, de számos eltéréssel az előző módszertől:
- A frekvenciatartomány 18 és 35 kHz között változik.
- Szerves oldószereket, például freont és etil-alkoholt használnak folyékony közegként.
- A stabil kavitációs folyamat fenntartásához és a munkadarab megbízható rögzítéséhez be kell állítani a fitomixer rezonancia üzemmódját, amelyben a folyadékoszlop az ultrahanghullám hosszának felének felel meg.
Ultrahanggal támogatott gyémántfúrás
A módszer egy forgó gyémántszerszám használatát foglalja magában, amelyet ultrahangos rezgések hajtanak meg. A kezelési folyamat energiaköltsége a hagyományos mechanikai eljárásokkal meghaladja a szükséges erőforrás mennyiségét, eléri a 2000 J/mm3 értéket. Ez a teljesítmény lehetővé teszi akár 25 mm átmérőjű fúrást 0,5 mm/perc sebességgel. Ezenkívül az anyagok fúrással történő ultrahangos feldolgozása hűtőfolyadékot igényel nagy mennyiségben, akár 5 l/percig. A folyadékáramlás a finom port is kimossa a szerszám és a munkadarab felületéről,a csiszolóanyag megsemmisülése során keletkezett.
Az RCD teljesítményének szabályozása
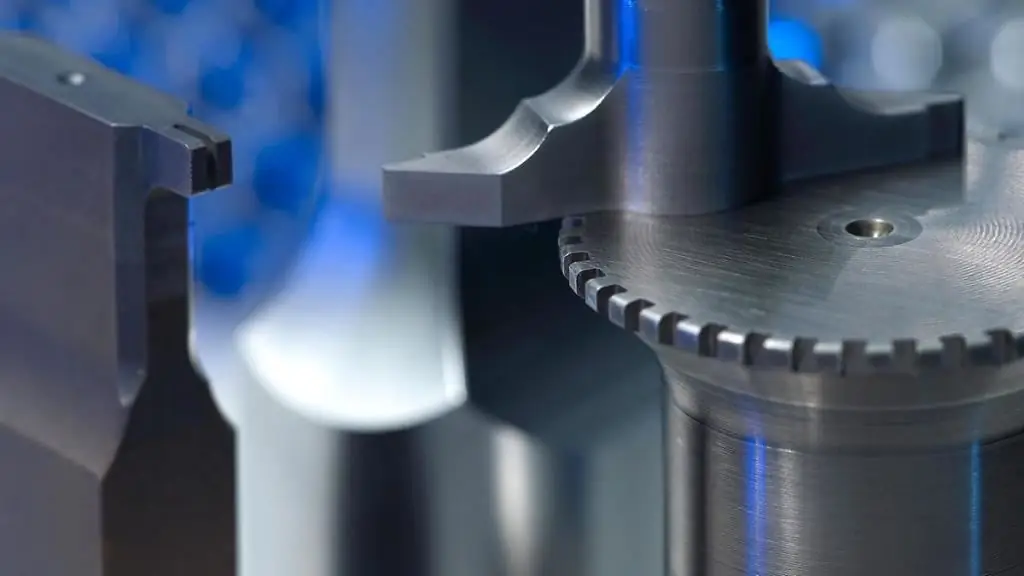
A technológiai folyamatot a kezelő irányítja, aki figyeli a ható rezgések paramétereit. Ez különösen vonatkozik az oszcillációk amplitúdójára, a hang sebességére, valamint az áramellátás intenzitására. Ezen adatok segítségével a munkakörnyezet és a csiszolóanyag munkadarabra gyakorolt hatásának ellenőrzése biztosított. Ez a tulajdonság különösen fontos a műszerek ultrahangos feldolgozásánál, amikor egy technológiai folyamat során több berendezés működési módja is alkalmazható. A legfejlettebb vezérlési módszerek magukban foglalják a feldolgozási paraméterek automatikus megváltoztatását a termék paramétereit rögzítő érzékelők leolvasása alapján.
Az ultrahangos technológia előnyei
Az RCD technológia használata számos előnnyel jár, amelyek a megvalósítás konkrét módjától függően eltérő mértékben jelentkeznek:
- A megmunkálási folyamat termelékenysége többszörösére nő.
- Az ultrahangos szerszámkopás 8-10-szeresére csökken a hagyományos megmunkálási módszerekhez képest.
- Fúráskor a feldolgozási paraméterek mélysége és átmérője nő.
- Növeli a mechanikai hatás pontosságát.
Technológiai hibák
A módszer széles körű alkalmazását még mindig számos hiányosság hátráltatja. Ezek elsősorban a szervezet technológiai összetettségéhez kapcsolódnak.folyamat. Ezenkívül az alkatrészek ultrahangos feldolgozása további műveleteket igényel, beleértve a csiszolóanyag szállítását a munkaterületre és a vízhűtéshez szükséges berendezések csatlakoztatását. Ezek a tényezők növelhetik a munka költségeit is. Az ipari folyamatok kiszolgálása során az energiaköltségek is emelkednek. További erőforrásokra van szükség nemcsak a főegységek működésének biztosításához, hanem az elektromos jeleket továbbító védelmi rendszerek és áramgyűjtők működéséhez is.
Következtetés
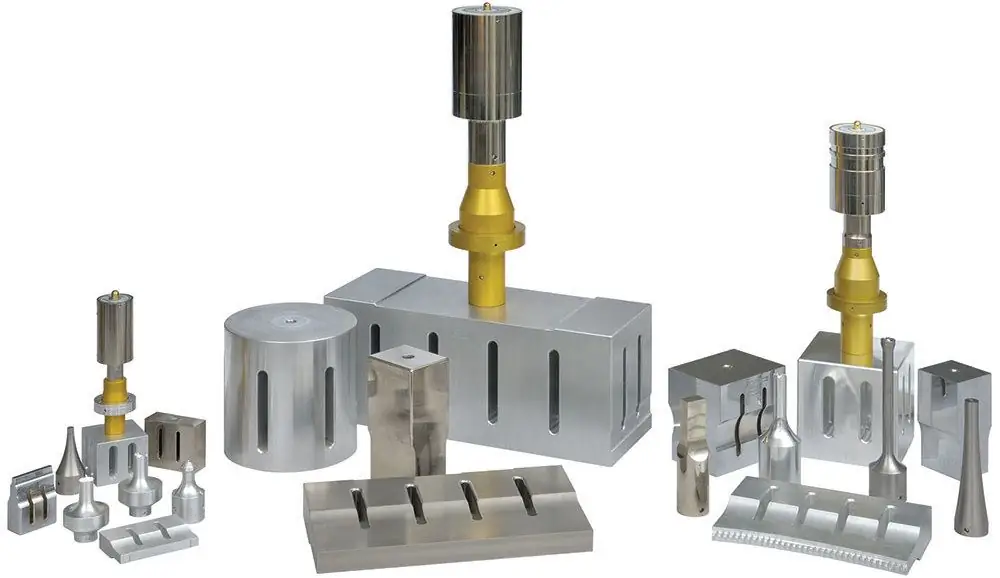
Az ultrahangos csiszolótechnológia bevezetése a fémmegmunkálási folyamatokban a hagyományos vágási, fúrási, esztergálási stb. módszerek alkalmazásának korlátai miatt következett be. A hagyományos esztergagépekkel ellentétben az ultrahangos fémmegmunkálás hatékonyan képes megbirkózni a megnövelt keménységű anyagokkal.. Ennek a technológiának a használata lehetővé tette edzett acélon, titán-karbid ötvözeteken, volfrámtartalmú termékeken stb. történő megmunkálási műveletek elvégzését. Ugyanakkor garantált a mechanikai hatás nagy pontossága a megmunkálási helyen található szerkezet minimális károsodásával. terület. De ahogy az más innovatív technológiák esetében is, mint például a plazmavágás, lézeres és vízsugaras feldolgozás, továbbra is vannak gazdasági és szervezeti problémák az ilyen fémfeldolgozási módszerek alkalmazásakor.
Ajánlott:
Plexigravírozás: előnyei és hátrányai, technológia, felszerelés
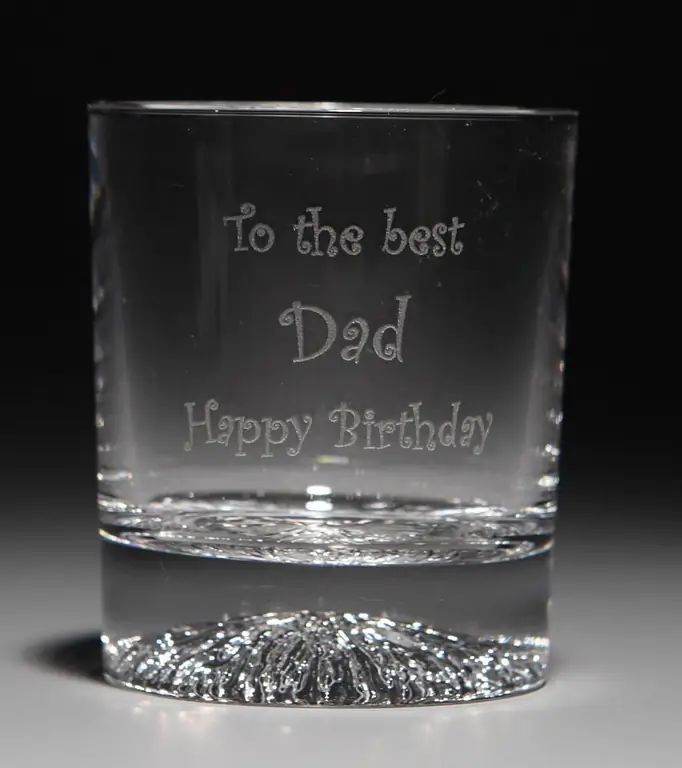
A pleximetszet festői mesterségnek számít. Finom művészi ízlést testesítenek meg a szuvenír figurák, ólomüveg ablakok vagy egy pompás rajzokkal díszített üvegasztal. A pácolás és a homokfúvás technológia a múlté. Manapság egy lézergép segítségével mindenki nagyon részletes mintát készíthet
A magasnyomás a Magasnyomásos nyomtatási technológia, a fejlesztés korszerű szakaszai, a szükséges felszerelések, az ilyen típusú nyomtatás előnyei és hátrányai
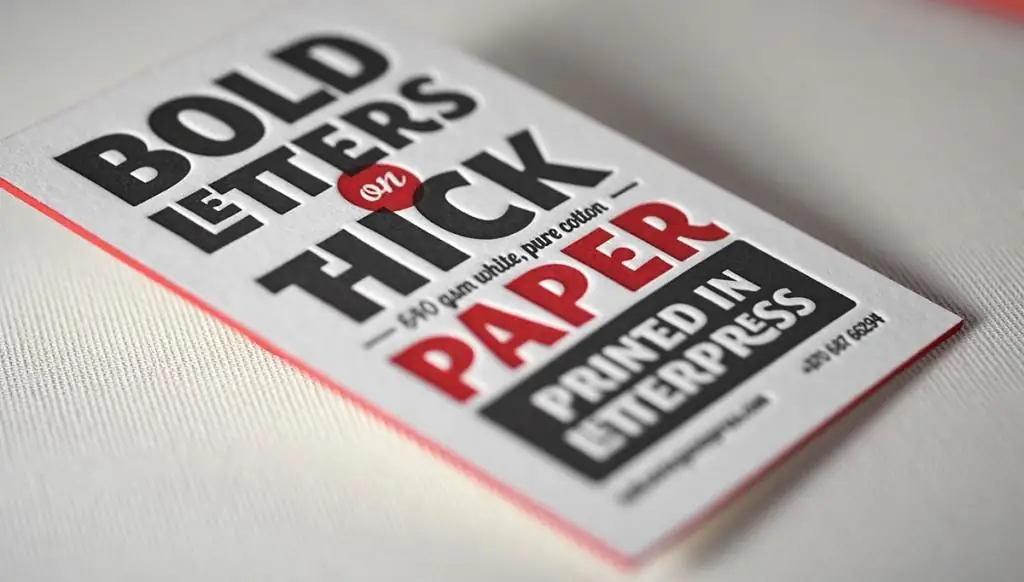
A magasnyomás az egyik tipikus módszer az információ dombormű-mátrix használatával történő alkalmazására. A kiálló elemeket paszta formájú festékkel bevonják, majd a papírhoz nyomják. Így különböző tömeges folyóiratok, segédkönyvek, könyvek és újságok sokszorosulnak
Ultrahangos műanyagok, műanyagok, fémek, polimer anyagok, alumínium profilok hegesztése. Ultrahangos hegesztés: technológia, káros tényezők
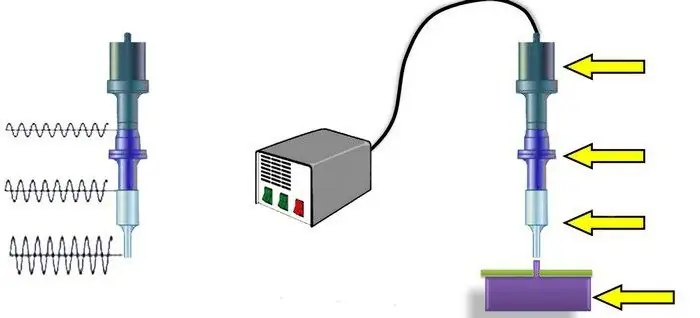
Fémek ultrahangos hegesztése olyan folyamat, amelynek során szilárd fázisban állandó kötés jön létre. A fiatalkori területek kialakulása (amelyekben kötések képződnek) és a köztük lévő érintkezés egy speciális eszköz hatására történik
Titán feldolgozás: az anyag kezdeti tulajdonságai, a feldolgozás nehézségei és típusai, működési elv, technikák és szakemberek ajánlásai

Ma az emberek sokféle anyagot dolgoznak fel. A titánfeldolgozás kiemelkedik a legproblémásabb munkatípusok közül. A fém kiváló tulajdonságokkal rendelkezik, de ezek miatt merül fel a legtöbb probléma
Elveszett viaszos öntés: technológia, előnyei és hátrányai
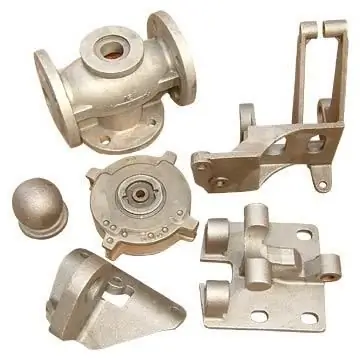
A befektetési modellek használata az öntödei termelés meglehetősen népszerű módja. Ott használatos, ahol szükséges a méretek pontos betartása és az alkatrészek felületének magas minősége. Így készülnek a turbinalapátok és a nagy teljesítményű szerszámok, műfogsorok és ékszerek, valamint az összetett konfigurációjú szobrok öntése. Az öntéshez használt forma egyrészes, az alacsony olvadáspontú anyagok modelljét a formázás során nem távolítják el, hanem kiolvasztják