2025 Szerző: Howard Calhoun | [email protected]. Utoljára módosítva: 2025-06-01 07:14
Minden vállalkozás vezetője tevékenységi területtől függetlenül arról álmodik, hogy növekedjen a profit és a termelési költségek változatlanok maradjanak. Ennek az eredménynek az elérését segíti a gyártásban lévő „5S” rendszer (az angol változatban az 5S), amely csak a belső tartalékok ésszerű felhasználásán alapul.
Ez a rendszer nem a semmiből jött létre. Valami hasonlót javasolt a 19. század végén az amerikai Frederick Taylor. Oroszországban ezt a tudós, forradalmár, filozófus és ideológus A. A. Bogdanov, aki 1911-ben könyvet adott ki a tudományos menedzsment elveiről. A benne fogl alt rendelkezések alapján a Szovjetunió bevezette a NEM-et, vagyis a munka tudományos szervezését. De a legtökéletesebb az 5C rendszer volt, amelyet Taiichi Ohno japán mérnök javasolt, és amelyet a Toyota Motor gyárában mutatott be. Mi ez, és miért lett olyan népszerű a japán rendszer?
A tény az, hogy egy egyszerű elven alapul, amely nem igényel költségeket. Abból álla következő - minden alkalmazottnak, a takarítótól az igazgatóig, a lehető legnagyobb mértékben optimalizálnia kell a részét az általános munkafolyamatban. Ez a termelés egészének nyereségének növekedéséhez és az összes alkalmazott jövedelmének növekedéséhez vezet. Az „5C” rendszer bevezetésének pálcáját most a világ minden tájáról vették fel a vállalkozások, köztük Oroszországot is. Ebben a cikkben megpróbáljuk meggyőzni a szkeptikusokat arról, hogy a japán know-how valóban működik, és minden tevékenységi területen.
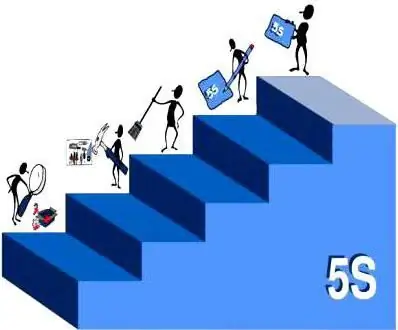
Az „5C” rendszer gyártásban, mi az?
Az International 5S jelentése öt lépés ("lépés" angolul step). Egyes közgazdászok és a munkához való új hozzáállás hirdetői a nevet az öt japán posztulátummal magyarázzák, amelyeket következetesen alkalmaznak az 5S rendszerben: seiri, seiton, seiso, seiketsu és shitsuke. Számunkra a natív „5C-k” közelebb állnak és érthetőbbek - öt egymást követő lépés, amelyet meg kell tenni termelésünk felvirágoztatása érdekében. Ez:
1. Rendezés.
2. A rend fenntartása.
3. Tisztaság tartása.
4. Szabványosítás.
5. Fejlesztés.
Amint láthatja, az "5C" rendszer nem igényel semmi természetfelettit a gyártás során. Talán ezért is lehet találkozni vele szemben bizalmatlansággal és komolytalan hozzáállással.
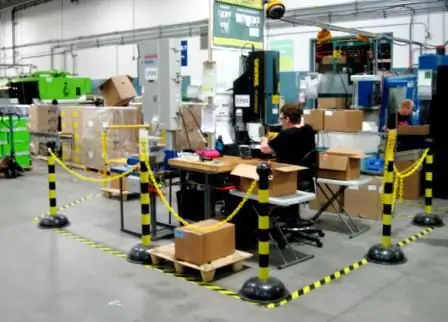
A rendszer létrehozásának szakaszai
A bölcs japán Taiichi Ohno, akinek a Toyota gyárban való bevezetésének köszönhetően sikerült felemelkedniemérnök vezérigazgatónak, észrevette, hogy mennyi veszteség keletkezik a különféle következetlenségek és átfedések miatt. Például néhány kis csavart nem tettek fel időben a szállítószalagra, és ennek következtében az egész gyártás leállt. Vagy fordítva, az alkatrészeket árréssel szállították, feleslegesnek bizonyultak, és emiatt az egyik alkalmazottnak vissza kellett vinnie a raktárba, ami azt jelenti, hogy üres munkára pazarolja az idejét. Taiichi Ohno kifejlesztett egy koncepciót, amelyet "éppen időben" nevezett. Vagyis pontosan annyi alkatrészt szállítottak a szállítószalagra, amennyi szükséges.
Más példákat is lehetne mondani. A gyártásban lévő „5S” rendszer tartalmazta a „kanban” fogalmát is, ami japánul „reklámtáblát” jelent. Taiichi Ohno azt javasolta, hogy minden egyes alkatrészhez vagy szerszámhoz csatoljanak egy úgynevezett "kanban" címkét, amelyben minden szükséges információ megtalálható az alkatrészről vagy szerszámról. Alapvetően mindenre vonatkozik. Például az irodában lévő árukra, gyógyszerekre, mappákra. A harmadik koncepció, amelyen az 5S rendszer a gyártásban alapul, a "kaizen" koncepciója, amely folyamatos fejlesztést jelent. Más koncepciók is születtek, amelyek csak nagyon speciális gyártási folyamatokhoz voltak alkalmasak. Ebben a cikkben nem foglalkozunk velük. A gyakorlatban kipróbált újítások eredményeként 5 olyan lépés alakult ki, amely bármely gyártásra alkalmazható. Elemezzük őket részletesen.
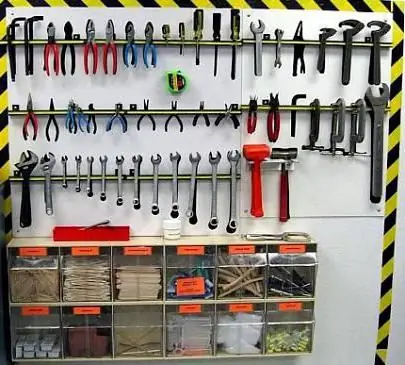
Rendezés
Sokunk asztali számítógépén vannak olyan elemek, amelyekbenalapvetően nem szükséges. Például régi nyomtatványok, fel nem használt fájlok, számítások piszkozatai, szalvéta, amelyen egy csésze kávé volt. És ebben a káoszban ott lehetnek a szükséges akták vagy dokumentumok. Az "5S" rendszer alapelvei a munkafolyamat optimalizálása, vagyis annak biztosítása, hogy az idő ne vesszen el a megfelelő dolgok keresésére a feleslegesek romjai között. Ez a válogatás. Vagyis a munkahelyen (a gép közelében, az asztalon, a műhelyben - bárhol) minden elemet két kupacba raknak - a szükségeseket és a feleslegeseket, amelyeket meg kell semmisíteni. Továbbá mindent, amire szüksége van, a következő halmokba bontják: „gyakran és folyamatosan használt”, „ritkán használt”, „majdnem nem használt”. Ezzel a rendezés befejeződött.
Rend tartása
Ha csak szétszedi az elemeket, semmi értelme. Ezeket a tárgyakat (szerszámokat, dokumentumokat) olyan sorrendbe kell rendezni, hogy az állandóan és gyakran használtak a szemünk előtt legyenek, vagy gyorsan elvihetőek és könnyen visszahelyezhetőek legyenek. Amit ritkán használnak, azt el lehet küldeni valahova dobozban, de rá kell ragasztani egy kanban címkét, hogy egy idő után könnyen és pontosan meg lehessen találni. Mint látható, az 5S rendszer a munkahelyen a legegyszerűbb lépésekkel kezdődik, de valójában nagyon hatékonynak bizonyul. Ráadásul javítja a hangulatot és a munkavágyat.
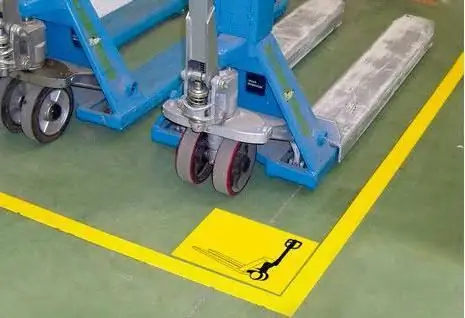
Tisztaság tartása
Ez a harmadik lépés sokak számára a leglogikusabb. Gyerekkorunktól kezdve tisztának tanítanak bennünket. Aa termelésben is szükséges, és ne csak az irodai dolgozók asztalai vagy a vendéglátó egységek szekrényei legyenek tiszták, hanem a gépek, a takarítók használati helyiségei is. Japánban az alkalmazottak gondosan ügyelnek a munkahelyükre, naponta háromszor takarítják őket - reggel munka előtt, ebédidőben és este, a munkanap végén. Vállalkozásaik emellett speciális területek jelölést vezettek be, amelyek lehetővé teszik számukra a gyártás során a rend betartását, vagyis a késztermékek területeit, bizonyos alkatrészek tárolását stb. különböző színekkel jelölik.
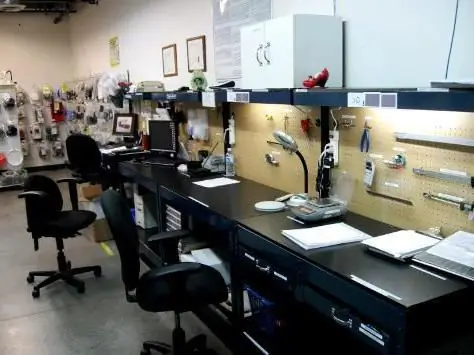
Szabványosítás
A szabványosítás alapelveit Taiichi Ohno találta ki. A modern 5S rendszer is széles körben alkalmazza őket. A termelésirányítás a szabványosításnak köszönhetően csodálatos eszközt kap az összes folyamat ellenőrzésére. Ennek eredményeként gyorsan kiküszöbölhetők az ütemtervből eredő késések okai, és kijavítják azokat a hibákat, amelyek rossz minőségű termékek kiadásához vezetnek. A Toyota Motor gyárban így nézett ki a szabványosítás: a művezetők napi munkaterveket készítettek, a munkahelyen pontos utasításokat helyeztek ki, a munkanap végén pedig speciális munkások ellenőrizték, hogy a nap folyamán milyen eltérések történtek a tervtől és miért. Ez a szabványosítás alapszabálya, vagyis a pontos utasítások, munkatervek és azok végrehajtásának ellenőrzése. Most sok vállalkozás, például az ENSTO észtországi üzeme, bónuszrendszert vezet be azon alkalmazottak számára, akik szigorúan betartják az 5C rendszer előírásait, és ennek alapján növelik termelékenységüket, amelynagy ösztönzést jelent, hogy ezt a rendszert életformaként fogadjuk el.
fejlesztés
Az ötödik lépés, amely befejezi az „5S” rendszert a gyártásban, a kaizen koncepción alapul. Ez azt jelenti, hogy beosztásától függetlenül minden dolgozónak törekednie kell a munkafolyamat javítására a rábízott területen. A kaizen filozófiai lényege, hogy az egész életünk napról napra jobbá válik, és mivel a munka az élet része, nem szabad elzárkózni a fejlesztésektől sem.
A tevékenységi kör itt széles, mert a tökéletességnek nincs határa. A japánok elképzelései szerint maguknak a munkásoknak kell fejleszteniük termelési folyamatukat, utasítások és kényszer nélkül. Jelenleg sok szervezet olyan dolgozókból álló csapatokat hoz létre, akik figyelemmel kísérik a termék minőségét, megtanítják másoknak pozitív tapasztalataikat, és segítenek a kiválóság elérésében.
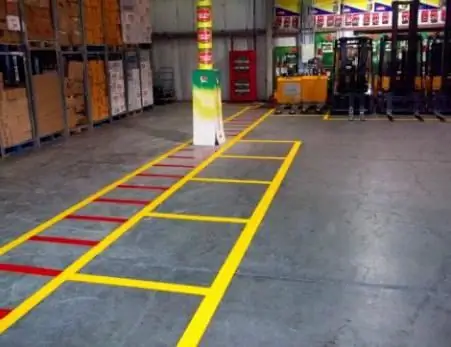
Alapvető hibák
Az "5C" rendszer működéséhez nem elég megszervezni vagy alkalmazottakat alkalmazni, akik rákényszerítik kollégáikat a megvalósításra. Fontos, hogy az emberek felismerjék ennek az innovációnak a hasznosságát, és életstílusként fogadják el. Az "5S" rendszer bevezetése Oroszországban a gyártásban éppen azért nehézségekbe ütközik, mert a mi orosz mentalitásunk eltér a japántól. Sok produkciónkra a következő jellemzők jellemzőek:
1. Az alkalmazottak, különösen, ha nincs rájuk ösztönző, nem törekednek a vállalkozás nyereségének növelésére. Azt kérdezik,miért kell a főnököt még gazdagabbá tenni, ha már mindene megvan.
2. Magukat a vezetőket nem érdekli az "5S" rendszer bevezetése, mert nem látják benne a célszerűséget.
3. Sok „felülről lefelé” utasítást csak a „pipálásra” szoktak végrehajtani. Japánban egészen más hozzáállás a munkájukhoz. Például ugyanaz a Taiichi Ohno, aki bevezette az "5S" rendszert, nem a személyes haszonra gondolt, hanem a vállalat hasznára, amelyben ő csak mérnök volt.
4. Sok vállalatnál erőszakkal vezetik be az 5S rendszert. A karcsú termelés, amely magában foglalja mindenféle veszteség (munkaidő, nyersanyagok, jó alkalmazottak, motiváció és egyéb mutatók) kiküszöbölését, nem működik, mivel a dolgozók tudatalatti szinten kezdenek ellenállni az innovációknak, ami végső soron minden erőfeszítést nullára csökkent..
5. A rendszert megvalósító menedzserek nem értik teljesen a lényegét, ami meghibásodásokat okoz a kialakult termelési folyamatokban.
6. A szabványosítás gyakran bürokráciává fejlődik, a jócselekedet benőtt olyan utasításokkal, utasításokkal, amelyek csak zavarják a munkát.
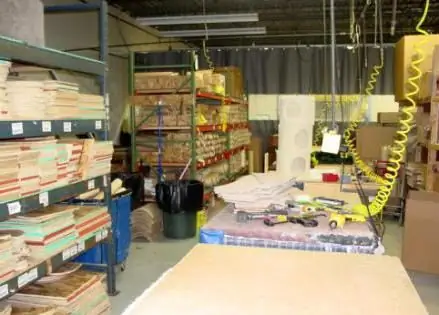
Vélemények
Azok az oroszok, akik bevezették az "5S" rendszert a gyártásba, az újítással kapcsolatos visszajelzések nagyon kétértelműek. Kiemelt előnyök:
- jobb a munkahelyen lenni;
- ne vonja el a figyelmet a munkáról felesleges apróságokkal;
- átláthatóbb munkafolyamat;
- a fáradtság csökkent a műszak végén;
- kissé nőttfizetés a munka termelékenységének növelésével;
- csökkent a foglalkozási sérülések száma.
Megjegyzett hátrányok:
- válogatáskor mindent kidobnak;
- a szabványosítás a bürokrácia növekedéséhez vezetett;
- Az „5C” rendszer bevezetése nem súlyosbította a problémákat a vállalkozás minden területén;
- Az 5S rendszer előtérbe helyezése olyan fontos problémákat háttérbe szorított, mint például a pótalkatrészek hiánya.
Ajánlott:
Vállalkozástervezési rendszer: módszerek és alapelvek
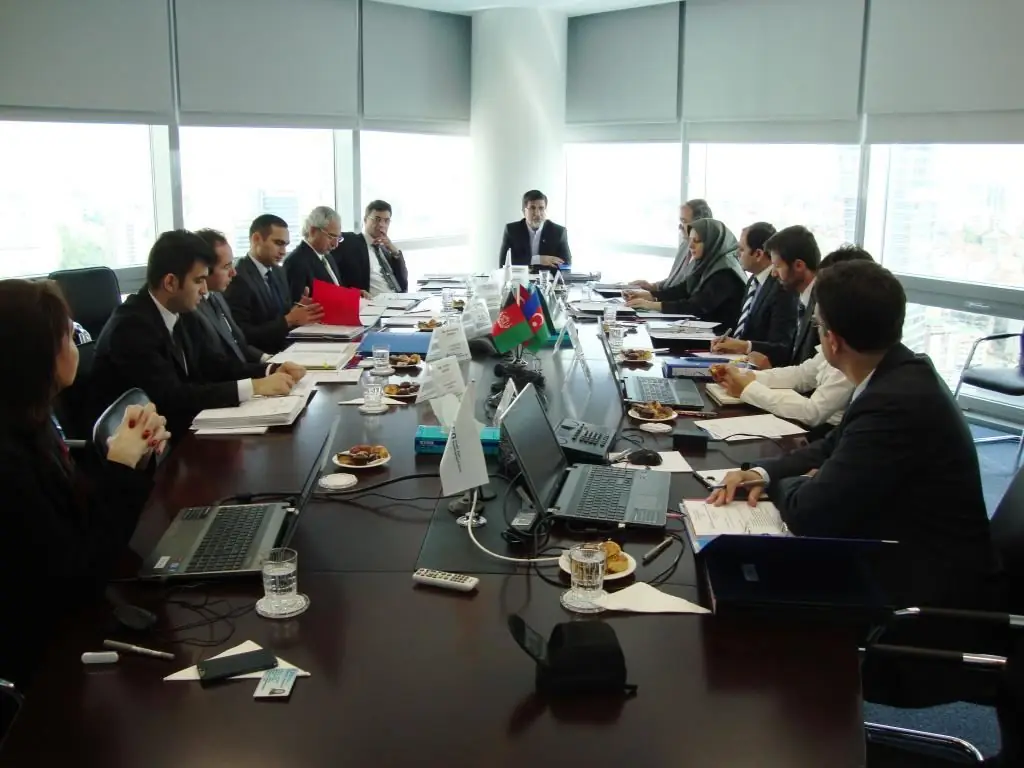
A tervezés vezetői funkció, melynek lényege, hogy az egyes részlegek, struktúrák számára meghatározza a fejlesztési stratégiát és feladatokat, melyek megvalósítása a választott stratégia követéséhez szükséges. A tervezés során nemcsak a vállalkozás céljait határozzák meg, hanem az időzítést és az elérésének módszereit is
A számvitel egy rendszer Definíció, típusok, feladatok és alapelvek
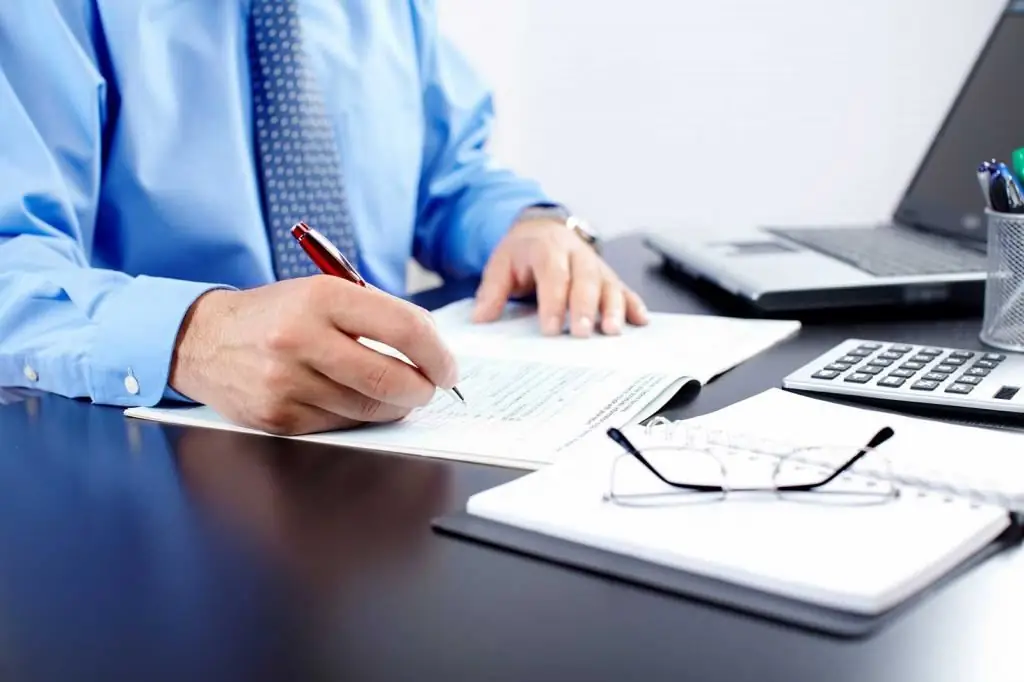
A számvitel egy rendezett típusú rendszer, amelynek célja az adatok pénzben kifejezett gyűjtése, rögzítése és összegzése minden gazdasági tranzakció dokumentált, folyamatos és folyamatos elszámolása révén. Ebben a cikkben megvizsgáljuk a kategória lényegét, jelentését és fajtáit. Emellett érintjük a számvitel alapelveit, feladatait
Paradicsom "Lady's Man": áttekintések, leírás, jellemzők, termesztési jellemzők
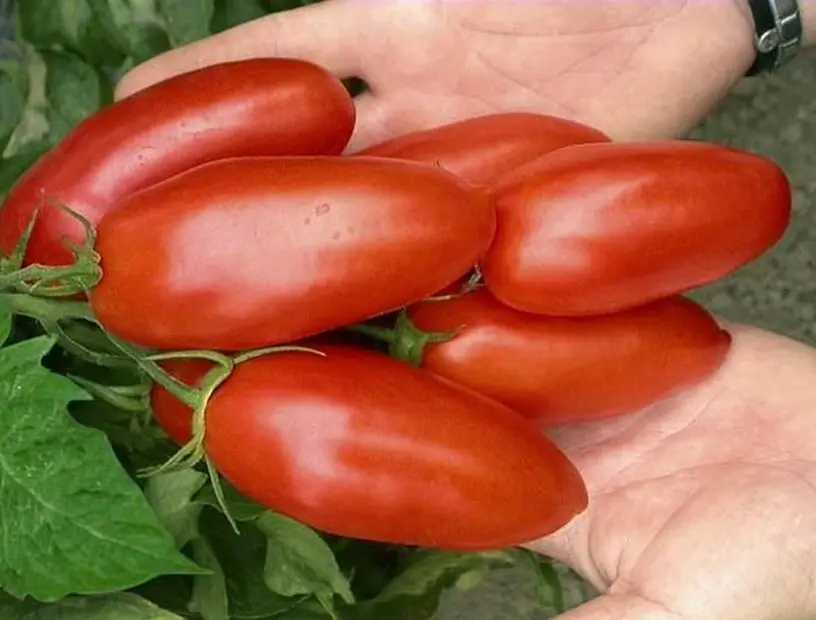
Ma a "Lady's Man" paradicsomfajta, amelynek véleménye rendkívül pozitív, vezető szerepet tölt be a korai érésű paradicsomok között. Az amatőr kertészek, akik legalább egyszer ültették az ágyásukat, mindig is rajongók maradtak."
"Kanban", gyártási rendszer: leírás, lényeg, funkciók és áttekintések
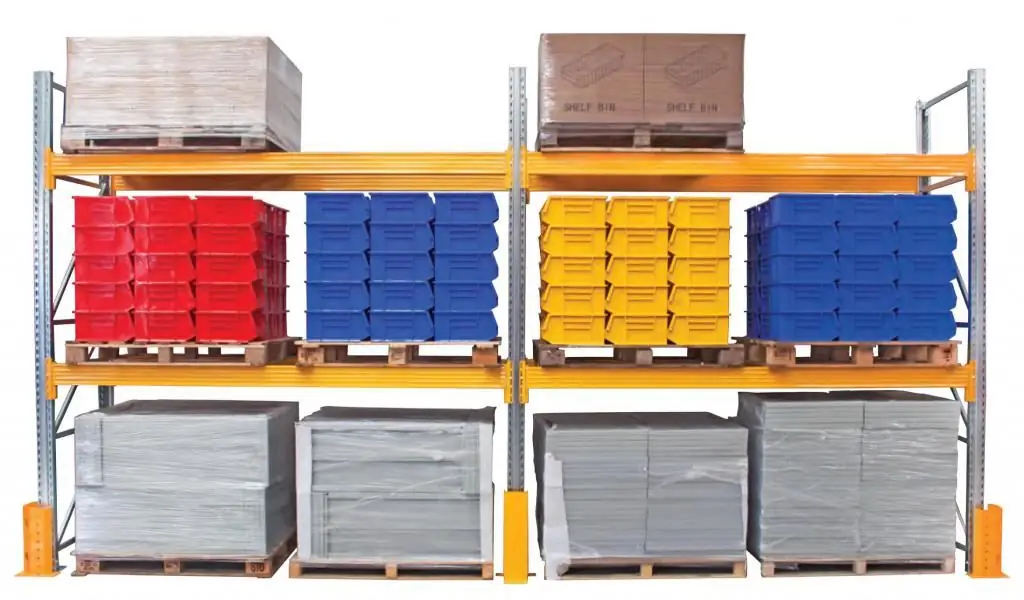
A Kanban a legismertebb ipari termelésirányítási módszer a Just-in-Time koncepción belül. Minimális szervezési költségekkel jelentősen csökkentheti a munkaidőt és az anyagi erőforrások költségeit
Keringető rendszer - leírás, telepítési jellemzők és áttekintések
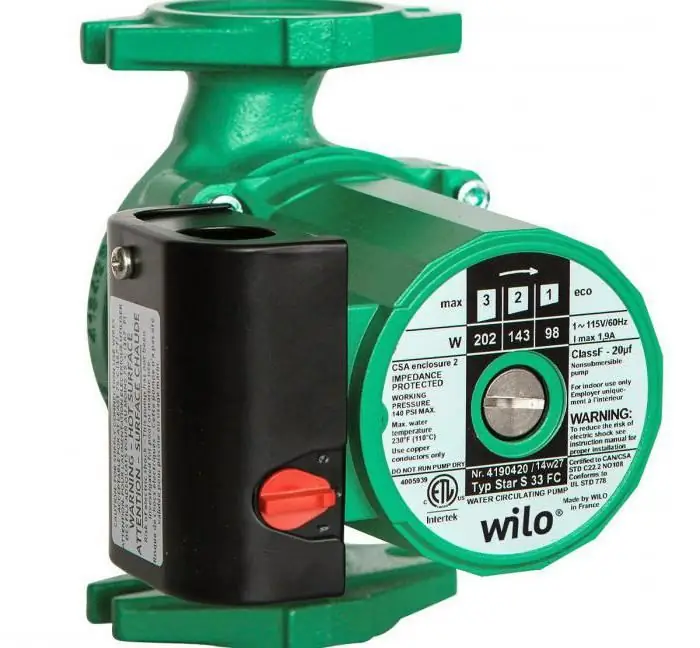
A cikk a keringési rendszerekkel foglalkozik. Figyelembe vették ennek a rendszernek az eszközét, valamint a szivattyú telepítésével kapcsolatos szerelési munkákat és az áttekintéseket