2025 Szerző: Howard Calhoun | [email protected]. Utoljára módosítva: 2025-06-01 07:14
A héjformába öntést héjöntésnek is nevezik. Külföldön pedig ezt a munkamódszert Shellnek hívják.
Általános információ
A mai ipari iparban sokféle öntési módszert alkalmaznak. A héjöntés mellett a befektetési öntést is alkalmazzák, valamint fémformákban és számos más módszert is alkalmaznak. Ezen öntési eljárások általános előnye a homoköntéssel összehasonlítva, hogy pontosabb véganyagokat eredményeznek mind forma, mind méretek tekintetében. Ezenkívül az ilyen termékek felületén az érdességek száma csökken. Ritkább esetben, de mégis előfordul, hogy az olvasztás utáni utólagos megmunkálás szükségessége megszűnik. Mindenek mellett a héjformás öntés és egyéb módszerek alkalmazása hozzájárul ahhoz, hogy ez a folyamat a lehető legnagyobb mértékben gépesíthető legyen, aminek következtében az automatizálása is megnő. És ez természetesen nagymértékben növeli bármely ipari létesítmény termelékenységét.
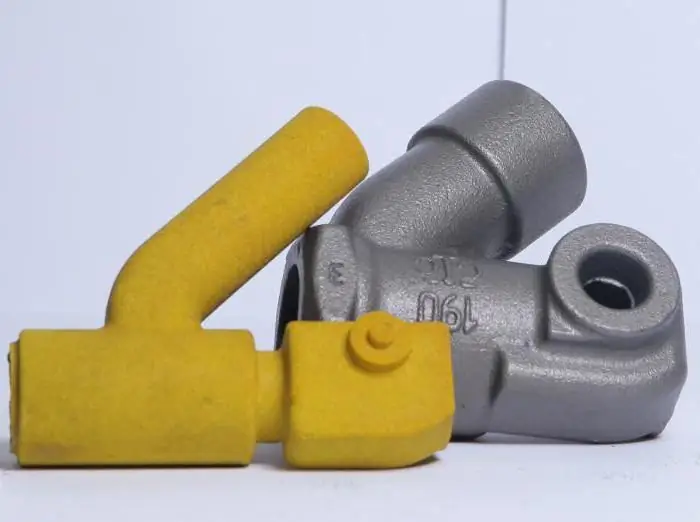
Shell-öntés
Ha konkrétan erről beszélünkmódszerrel, először 1953-ban vezették be a gyárakban. Jelenleg a módszert meglehetősen széles körben alkalmazzák. A Kirovets traktor alkatrészeinek nagy részét például a kagylóformákba öntéssel állítják elő. Minden alkatrész, amelyet ezzel a módszerrel gyártanak, a legjobb minőségű acélból vagy öntöttvasból készül. A héjöntés olyan módszer, amelyben az öntés végeredménye két homok-gyanta héjból álló alakot kap. Ezenkívül az alkatrészek gyártásának ezt a módszerét csak olyan esetekben használják, amikor kis vagy közepes méretű, de ugyanakkor nagy pontosságú alkatrészt kell létrehozni. Ennek az öntési módszernek a példái a motoralkatrészek vagy a vékonyfalú öntvények.
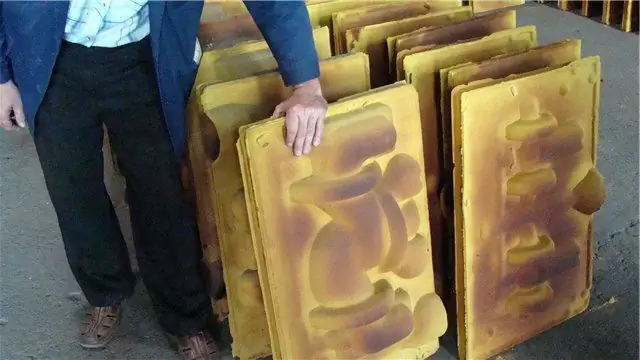
Az Út lényege
Ezzel a munkamódszerrel különféle alkatrészeket szerezhet be ventilátorokhoz, motorokhoz, szivattyúkhoz vagy textilipari gépekhez. Az átvett termék maximális hossza azonban nem haladhatja meg az 1 métert, és nem lehet nehezebb 200 kg-nál.
A héjformákba öntés lényege a hőre keményedő gyanták bizonyos tulajdonságain alapul, amelyek a homok-gyanta keverékek részét képezik. Az ilyen komponensek használatának előnye, hogy ezek a gyanták gyorsan és tartósan megkeményednek, ha 200-250 Celsius fokos hőmérsékleten kezelik.
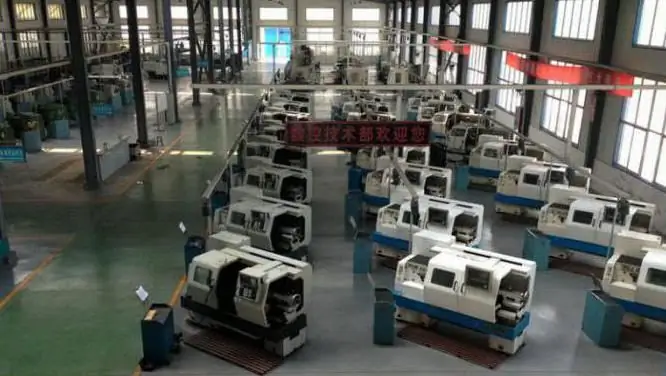
Kagylóforma készítése öntéshez
A utólagos öntéshez szükséges öntőforma készítéséhez finomszemcsés kvarchomok szükséges, amelyhez hőre keményedő gyanta is jár, amely összekötő eleme a teljes értékű héjforma kialakításához. Ezeket az anyagokat, különösen a gyantát azért választják, mert megkeményednek, amikor áthaladnak egy bizonyos hőmérsékleti korláton. A gyártási folyamat a következő. Először a gyantát 140-160 Celsius fokra melegítjük. Ilyen környezet hatására folyékony ragasztómasszává alakul, amely teljesen beborítja a kvarchomok formát.
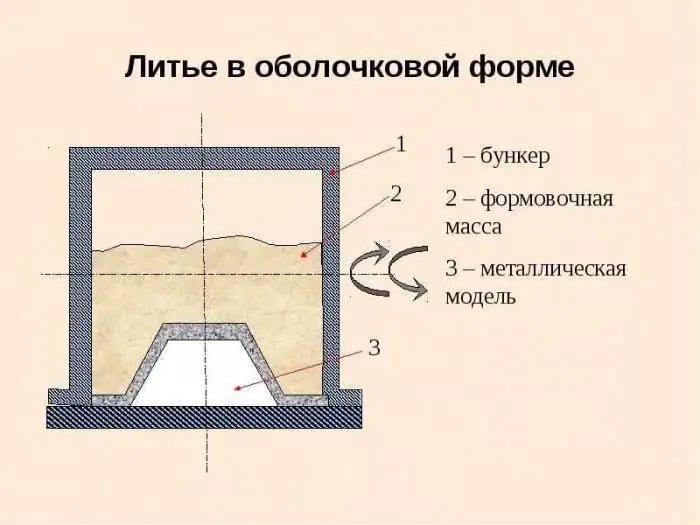
A héjformákban történő öntés hatóköre meglehetősen széles, ezért az öntőformák gyártási folyamata automatikus vagy automatizált.
Miután a formát teljesen beborította a gyantával, a hőmérsékletet 200-250 Celsius-fokra emeljük. Ez a hőmérsékleti küszöb elégséges ahhoz, hogy a ragasztómassza visszafordíthatatlanul megszilárduljon és formát alkosson. Továbbá, amikor az alkatrészek öntési folyamata megkezdődik, vagyis amikor az olvadt fém belép a formába, a hőmérséklet eléri a 600 fokot. Ez az üzemmód elegendő annak biztosítására, hogy a gyanta ne olvadjon meg, hanem kiégjen, miközben magán a formán hagy pórusokat, ami megkönnyíti a gázok távozását.
A héjformás öntés előnyei és hátrányai
Mint minden más gyártási folyamatnak, ennek is megvannak az előnyei és hátrányai. Ha összehasonlítjuk ezt az öntési módot például a beöntésselA hagyományos homokformáknak számos előnye van:
- Az első és meglehetősen jelentős különbség a pontossági osztály, amely 7-9. Ezenkívül a kapott alkatrész felületi minősége 3-6-ig javul. Ezenkívül csökkennek a ráhagyások, amelyek a kapott alkatrész öntés utáni utólagos megmunkálásához megengedettek.
- Az egyik nagy előny az öntvénygyártás munkaerőköltségének jelentős csökkenése.
- Ez az öntési módszer csökkenti az öntőanyag-felhasználást, valamint a fém mennyiségét, mivel a kapucsatornák mérete csökken.
- Jelentősen csökkentette a házasságkötések számát.
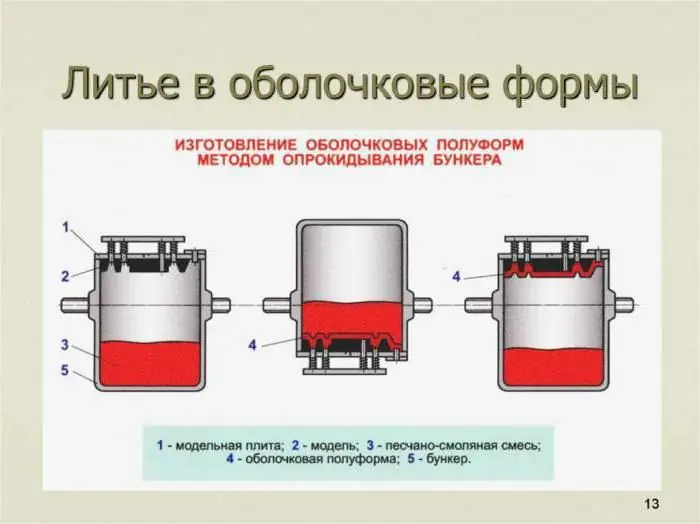
A héjformákban történő öntésnek azonban van néhány hátránya. Ezek a következők:
- Héjforma élettartama - 1 öntés.
- A homok fröccsöntésének költsége meglehetősen magas.
- A káros gázok magas százaléka.
Korpuszképzési folyamat
A testformáló folyamat hat szakaszban zajlik:
- Az első lépésben a keveréket forró fémmodellre öntjük, valamint több tíz másodpercig tartjuk, amíg vékony, erős kéreg nem képződik az alkatrész körül. A modellek leggyakrabban öntöttvasból készülnek, és hevítésüket 230-315 fokig végzik.
- Ezt követően el kell végezni egy műveletet a felesleges formázóhomok eltávolítására. A kéreg vastagságának végül 10 és 20 között kell lenniemm. Ez függ a keverék tartózkodási idejétől a modellen, valamint a hőmérséklettől.
- Ezt követően a modelllapot a formával együtt át kell vinni a sütőbe, ahol a kikeményedés végéig ott lesznek. Az eljárás végén a héj szilárdságának 2,4 és 3,1 MPa között kell lennie.
- A kemencéből való kivétel után az edzett héj elmozdul a lemezről. Ehhez az eljáráshoz speciális tolót használnak.
- Ezt követően két vagy több modellt rögzítenek egymáshoz valamilyen bilinccsel vagy ragasztással. Ezek a formák héjformákban történő öntéshez vagy egyszerűen tárolhatók. Szinte korlátlan eltarthatóság.
- Mielőtt megkezdődik az öntési folyamat a kész formában, sörétet öntenek beléjük, ami segít megelőzni vagy tönkretenni a formát a további öntés során.
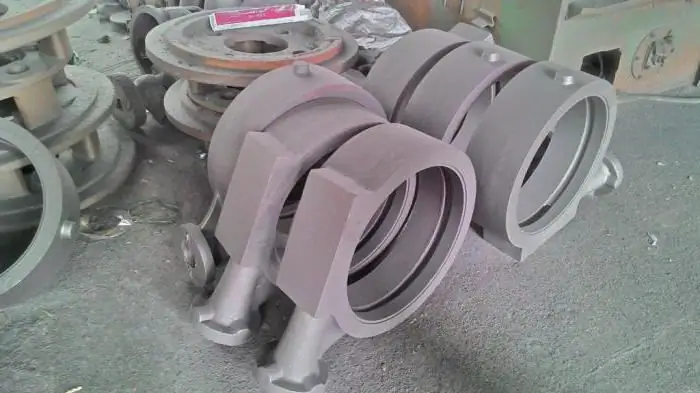
Átküldés részletei
Érdemes azzal kezdeni, hogy a szerszámok gyártásánál megengedett tipikus tűrés 0,5 mm lehet. A felületi érdesség 0,3 és 0,4 mikron közötti tartományban megengedett. Az ilyen határértékeket az a tény indokolja, hogy finom szemcsés homokot használnak. Érdemes megjegyezni: a gyanta használata nagyban hozzájárul ahhoz, hogy a felület nagyon sima legyen.
Gyártási mennyiségek
Ahhoz, hogy ilyen formák és alkatrészek gyártásával foglalkozhasson, gondoskodni kell egy formamodell beszereléséről. A telepítéshez szükséges idő kevesebb, mint egy hét. A telepítés befejezése után a kimeneti mennyiség lehetelérheti az 5-50 darabot óránként. Az ilyen termelési mennyiségek óránként meglehetősen valósak, ehhez azonban az öntési folyamatot ennek megfelelően elő kell készíteni. Az öntéshez szükséges fő anyagok az öntöttvas, alumínium, réz, valamint az ilyen típusú fémek ötvözetei. Egy másik szükséges anyag egy alumíniumot és magnéziumot használó ötvözet.
Ajánlott:
A hitelbővítés a hiteltranzakciók és a banki műveletek intenzív bővítése profitszerzés céljából
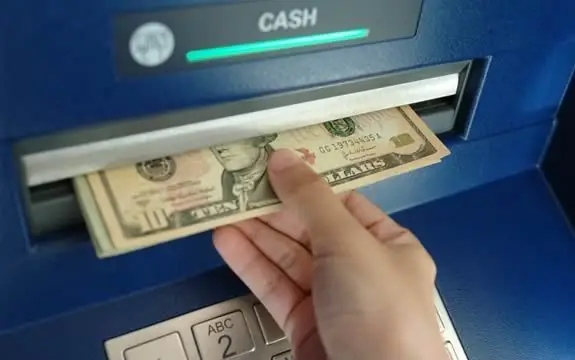
A hitelexpanzió a monetáris hitelpolitika egy fajtája, amelynek lényege a jövedelmezőség növelése a befolyási övezetek kiterjesztésével és a banki tevékenység élénkítésével. Maga a szó azt jelenti, hogy „terjeszkedni vagy terjedni”. Ezek az értékek meghatározóak az egész folyamatra nézve, melynek fő célja a szolgáltatások, befektetések és nyersanyagok jövedelmező piacáért való küzdelem
Logisztikai műveletek: koncepció, jellemzők, típusok
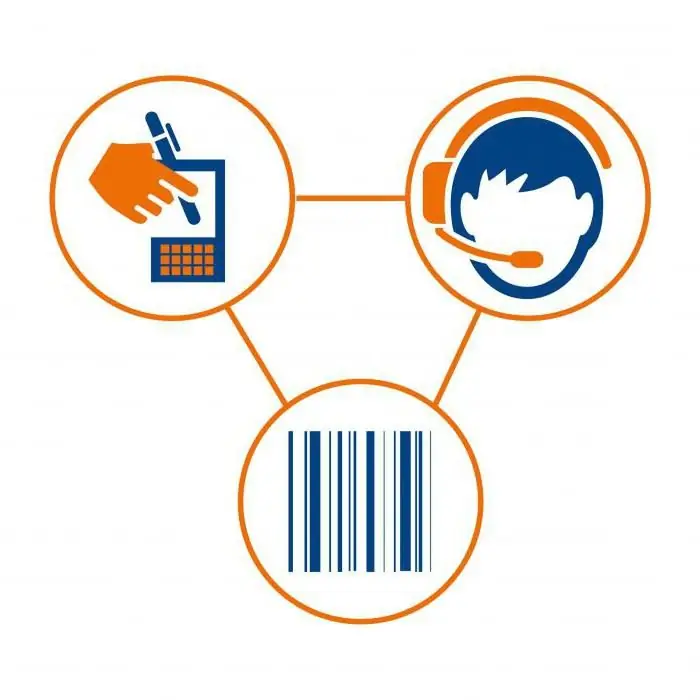
A cikk a logisztikai műveleteket és azokat a funkciókat tárgyalja, amelyeket a modern termelés körülményei között ellátnak
Öntés szilikon formába: felszerelés. Vákuumos öntés szilikon formákban
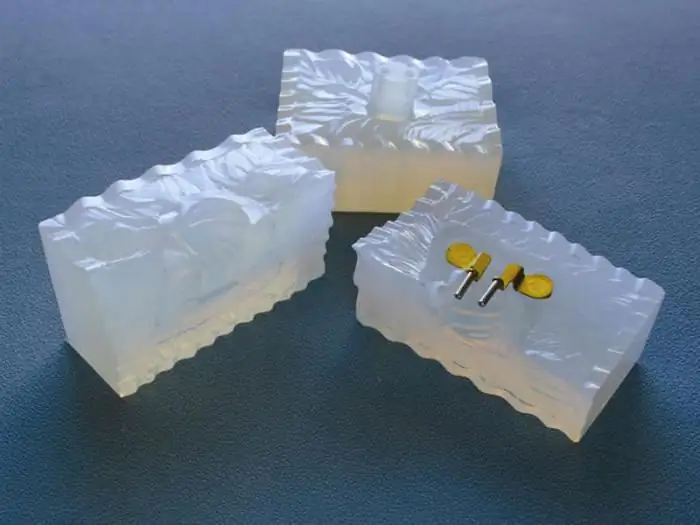
Kis számú műanyag nyersdarab gyártásához leggyakrabban szilikonformákba vákuumöntést alkalmaznak. Ez a módszer meglehetősen gazdaságos (a fémforma elkészítése több időt és pénzt igényel). Ezenkívül a szilikon formákat többször is használják, és ez jelentősen csökkenti az előállítási költségeket is
Centrifugális öntés – módszer precíz munkadarabok előállítására
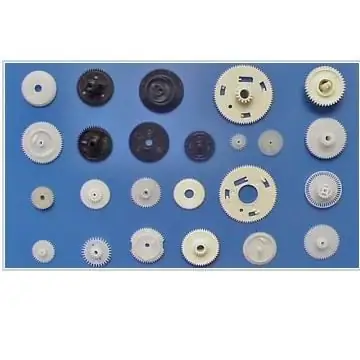
A centrifugális öntvénynek számos előnye van: az üreges héjak és salakzárványok hiánya a keletkező öntvényben, nagy anyagsűrűség, a fém megnövekedett kopásállósága, ami az egységes szerkezetnek köszönhetően érhető el stb
Elveszett viaszos öntés: technológia, előnyei és hátrányai
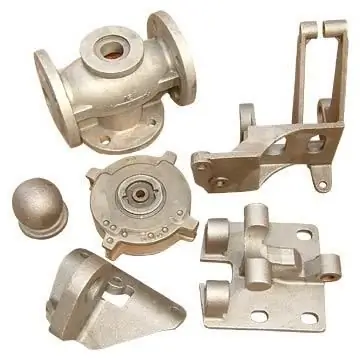
A befektetési modellek használata az öntödei termelés meglehetősen népszerű módja. Ott használatos, ahol szükséges a méretek pontos betartása és az alkatrészek felületének magas minősége. Így készülnek a turbinalapátok és a nagy teljesítményű szerszámok, műfogsorok és ékszerek, valamint az összetett konfigurációjú szobrok öntése. Az öntéshez használt forma egyrészes, az alacsony olvadáspontú anyagok modelljét a formázás során nem távolítják el, hanem kiolvasztják