2025 Szerző: Howard Calhoun | [email protected]. Utoljára módosítva: 2025-01-24 13:17
Ma már rengeteg különféle dolog, alkatrész stb. készül acélból, ehhez természetesen nagy mennyiségű alapanyagra van szükség. Ezért az üzemekben régóta alkalmazzák az acél folyamatos öntésének módszerét, amelyet a legfontosabb jellemző - a magas termelékenység jellemez.
A munkához elengedhetetlen felszerelés
A mai napig számos olyan berendezés ismert, amelyek ilyen módon öntik acélt, és ezek rövidítése UNRS. Kezdetben egy vertikális típusú installációt fejlesztettek ki és helyeztek üzembe, amely 20-30 méterrel a műhelypadló szintje alatt helyezkedett el. Később azonban a padlómélyítés elhagyásának vágya vált ezen létesítmények fejlesztésének fő motorjává. Ez vezetett a torony típusú folyamatos öntőművek kifejlesztéséhez és megvalósításához. Ezeknek a berendezéseknek a magassága 40 m volt, azonban a gép ezen változatát két okból nem alkalmazták széles körben. Először is építsegy ilyen egység a műhelyben meglehetősen problémás és fáradságos. Másodszor, még több nehézség adódott a működésével kapcsolatban.
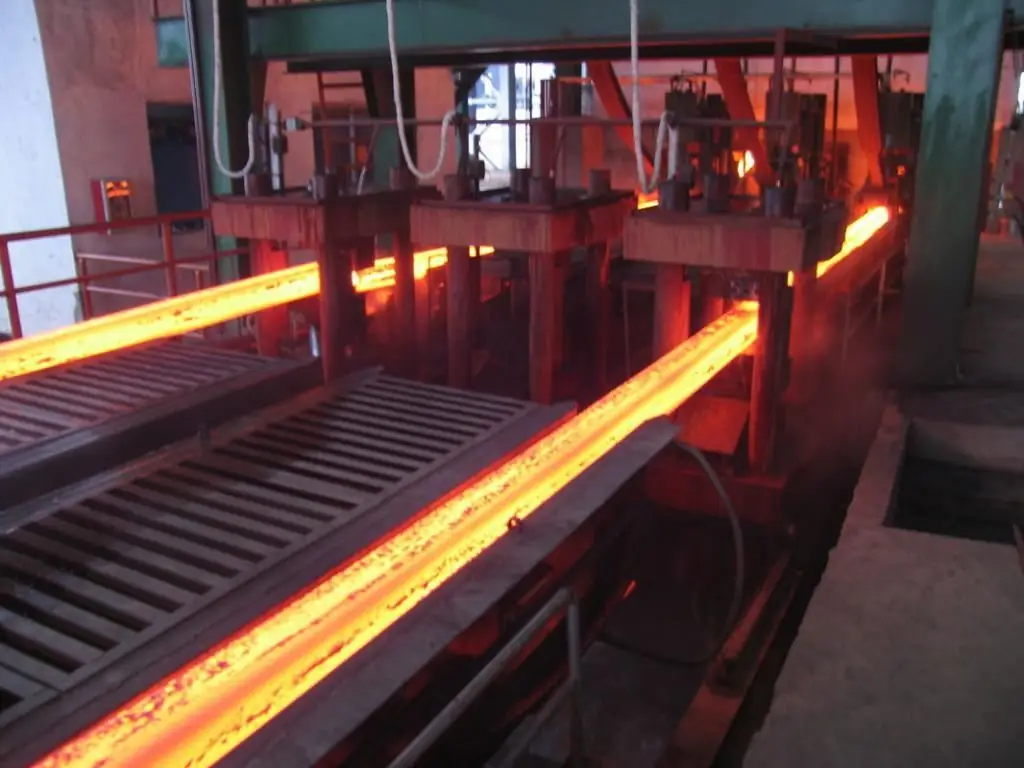
Íves és sugárirányú telepítések
Idővel az acél folyamatos öntése átkerült a függőleges hajlítógépekhez. A fő jellemző a tengelyek után kilépő tuskó 90 fokos meghajlítása. Ezt követően a beépítésnél speciális egyengető mechanizmust alkalmaztak a tuskó kiegyenesítésére, és csak ezen szakasz után került sor a vágásra. Az acél folyamatos öntése ilyen berendezéseken valamiért nem vált túl népszerűvé. Először is, a kanyar természetesen lehetővé tette a magasság csökkentését, ugyanakkor erősen korlátozta magának a tuskó keresztmetszetét. Minél nagyobb volt az anyag egy szakaszának beszerzése, annál nagyobbnak kellett lennie a hajlításnak, ami azt jelenti, hogy a magasság ismét nőtt. Másodszor, a hajlítógépeket az acélműhelyekben még nagyobb nehézségekkel helyezték el, mint a függőlegeseket.
Ma egyre népszerűbbek a radiális acél folyamatos öntésére szolgáló berendezések. Egy ilyen egységen a tömb az öntőformában képződik, és ugyanazon az íven hagyja el, amely mentén belépett. Ezt követően egy húzáskorrekt mechanizmussal kiegyenesítik. És akkor már kezdheti is a tuskó darabolását. Ez a kialakítás bizonyult a gyakorlatban a legracionálisabbnak az acélműhely áruáramlásának megszervezésében.
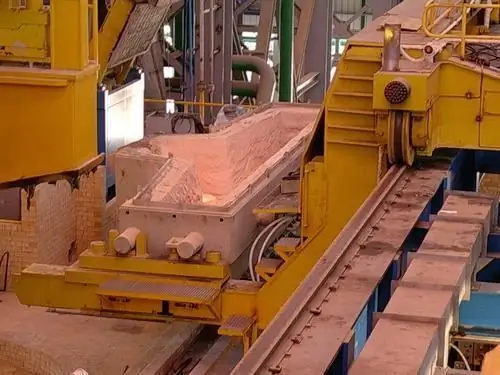
Hol kezdődik a casting
A folyamatos technológiájaAz acélöntés meglehetősen bonyolult folyamat. Mindazonáltal méltányos azt mondani, hogy az elv ugyanaz marad, függetlenül a használt gyártási beállítástól. Megfontolhatja a technológiát egy függőleges UNRS példáján.
A géphez egy merőkanál tartozik az acél egy speciális daru segítségével történő öntéséhez. Ezt követően az acél az elosztó edénybe folyik, amely dugóval rendelkezik. Az egyszálú gépeknél egy dugó, a többszálú gépeknél folyamonként egy dugó lesz. Ezen kívül az elosztó edényben van egy speciális terelőlemez is, amely a salakot tartja. Az elosztóedényből az acél az adagolóüvegen vagy egy dugón áthaladva a formába áramlik. Itt fontos megjegyezni, hogy az első öntés előtt a magot az alsó oldalról juttatják a formába. Vagy a teljes forma keresztmetszetét tölti ki, vagy csak a munkadarab alakját. A mag felső rétege a forma alja lesz. Ezenkívül fecskefarok alakú is van, hogy a jövőben lehessen rákapcsolni egy rúddal.
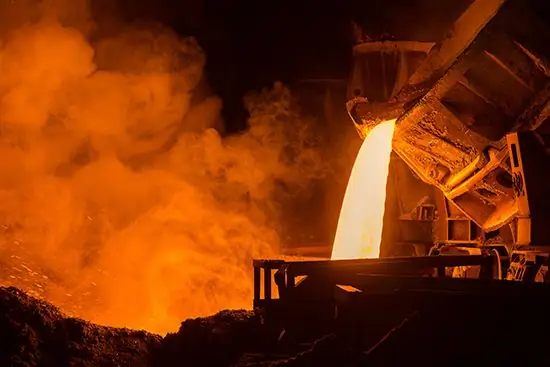
További casting
Ezután az acél folyamatos öntése során meg kell várni, amíg a nyersanyag szintje a mag fölé emelkedik kb. 300-400 mm magasságig. Amikor ez megtörténik, elindul a mechanizmus, amely működésbe hozza a húzószerkezetet. Húzóhengerekkel rendelkezik, amelyek hatására a mag leesik, és magával húzza a keletkezett tuskót.
A folyamatos öntőgépnek általában rézből készült formája van, üreges falakkal. Intenzív állapotban vanhűtővíz hatására, és belső metszete megfelel az előállítandó tuskó alakjának. Itt jön létre a tuskó-blank kéreg. Nagy öntési sebességnél ez a kéreg elszakadhat és a fém szivároghat. Ennek elkerülése érdekében a penészt egymás után mozgó mozgások jellemzik.
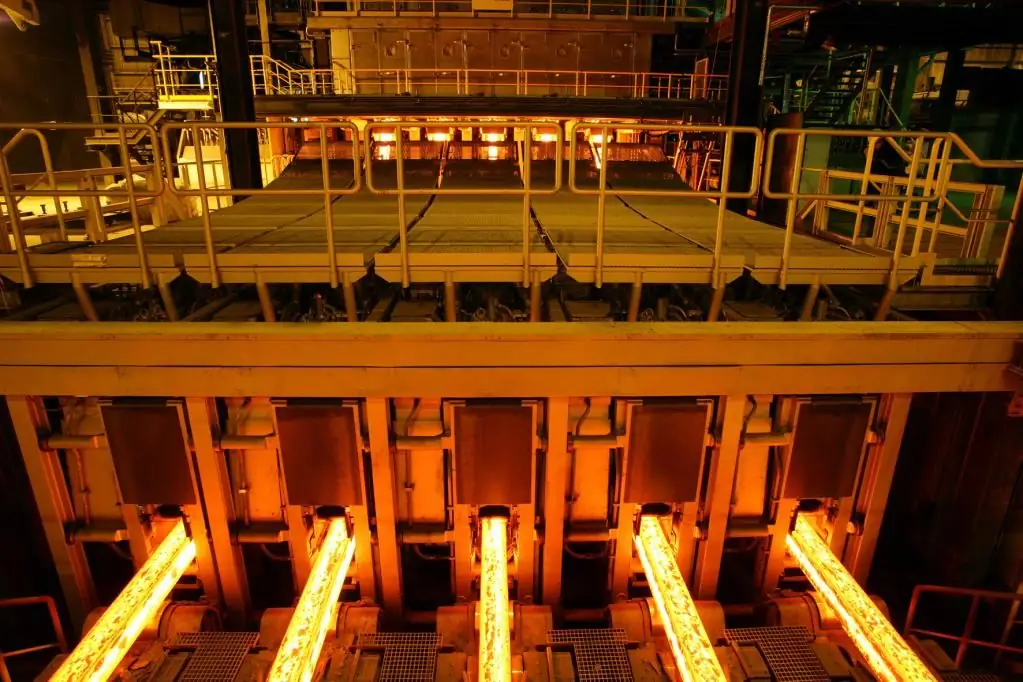
Az öntőforma működésének jellemzői
A folyamatos öntőgép egy villanymotorral rendelkezik, amely felelős ennek az oda-vissza mozgásnak a létrehozásáért. Ez a sebességváltó erejével, bütykös lengőmechanizmussal történik. Először az öntőforma a munkadarabbal megegyező irányba mozog, azaz lefelé, majd a folyamat befejezése után visszaáll felfelé. A lengési löket 10-40 mm. A forma fontos rekesz az acél folyamatos öntésében bármilyen típusú berendezésen, ezért falait paraffinnal vagy bármilyen más, a jellemzőknek megfelelő kenőanyaggal kenik.
Érdemes megjegyezni, hogy a modern berendezésekben a fémszintet radiometriai úton szabályozzák, vezérlőjellel az üst ütközőjére. Magában a formában semleges vagy redukáló atmoszférát lehet létrehozni a fémszint felett, hogy elkerüljük a termék oxidációját a gyártás során.
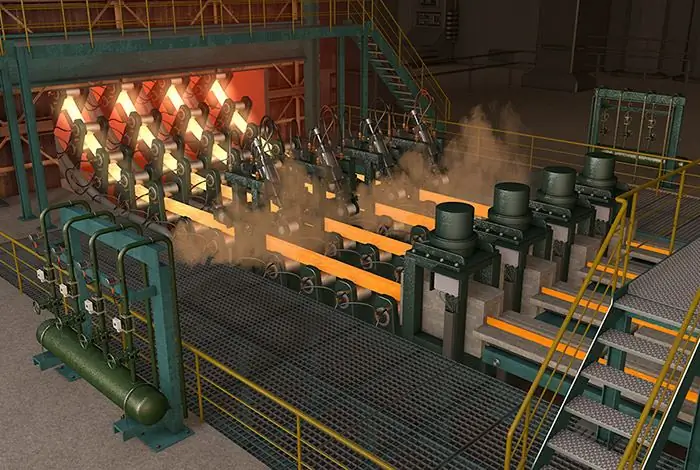
Bugcsípő
Érdemes megjegyezni, hogy a vákuum alatti munka is ígéretes öntési módszernek számít. Egy egység képes végrehajtaniegyszerre több formán keresztül önteni. Így egy telepítés adatfolyamainak száma elérheti a nyolcat is.
A hideg mag hűtőbordája a tuskóhéj aljának kialakítására szolgál. A tömb a másodlagos hűtési zónába (SCZ) beszívott mag hatására kilép a formából. A tuskó közepén az acél továbbra is folyékony állapotban lesz. Itt fontos megjegyezni, hogy az acélöntési technológia követelményei szerint a héjvastagságnak a formából való kilépéskor legalább 25 mm-nek kell lennie. Ezen követelmények teljesítéséhez szükséges a megfelelő anyagáramlási sebesség kiválasztása.
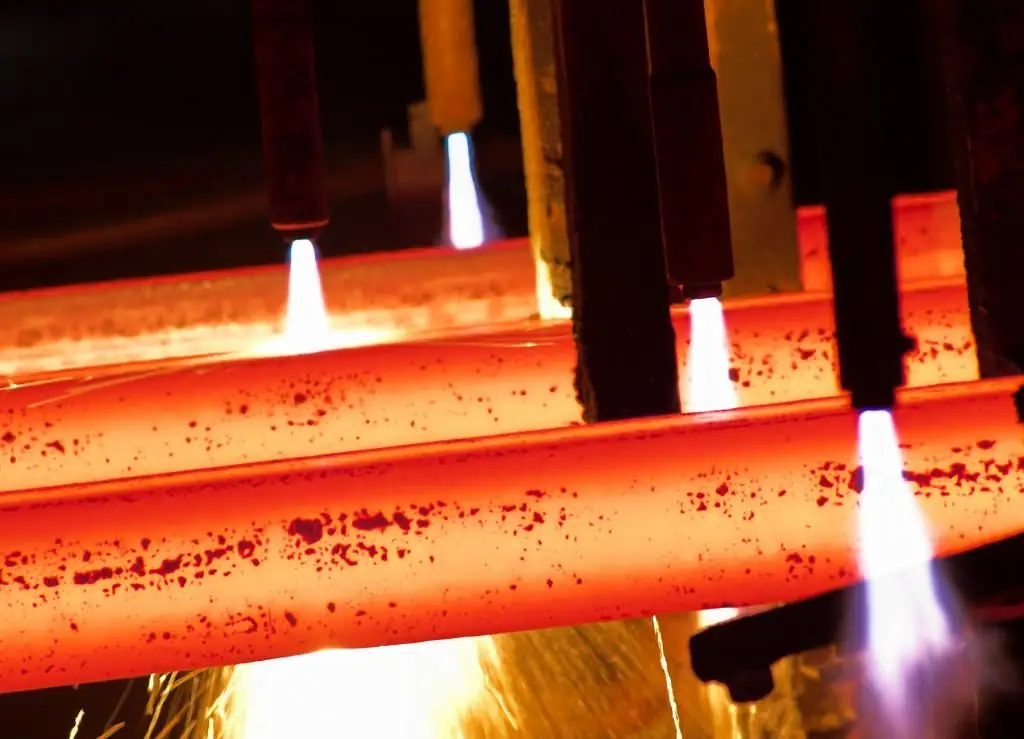
A telepítési és öntési folyamat jellemzői
A technológiai jellemzők körülbelül a következők. Ha a tuskó keresztmetszete 160x900 mm, akkor a sebessége 0,6-0,9 m/perc legyen. Ha a keresztmetszet 180x1000 mm, akkor a sebesség 0,55-0,85 m / percre csökken. A legnagyobb sebességjelző a négyzet alakú tuskó keresztmetszete esetén szükséges 200x200 mm - 0,8-1,2 m/perc.
A fenti mutatók alapján megállapíthatjuk, hogy egy szál átlagos öntési sebessége folyamatos öntési technológiával 44,2 t/h. Ha túllépi az optimális sebességet, akkor a központi porozitás megnő.
Továbbá érdemes megjegyezni, hogy az öntvény stabilitását és magának a terméknek a minőségét befolyásolja a fém hőmérséklete. Tapasztalatilag azt találták, hogy több mint 1560 fokos hőmérsékletenCelsius fokban a tuskó felületét gyakran repedések borítják. Ha a hőmérséklet alacsonyabb a jelzettnél, akkor az üveg gyakran megfeszül. Így azt találták, hogy az acél folyamatos öntésének módszeréhez az optimális hőmérséklet 1540-1560 Celsius fok. Ennek a mutatónak a fenntartása érdekében a kemence fűtési hőmérsékletének kibocsátás előtt 1630-1650 fok között kell lennie.
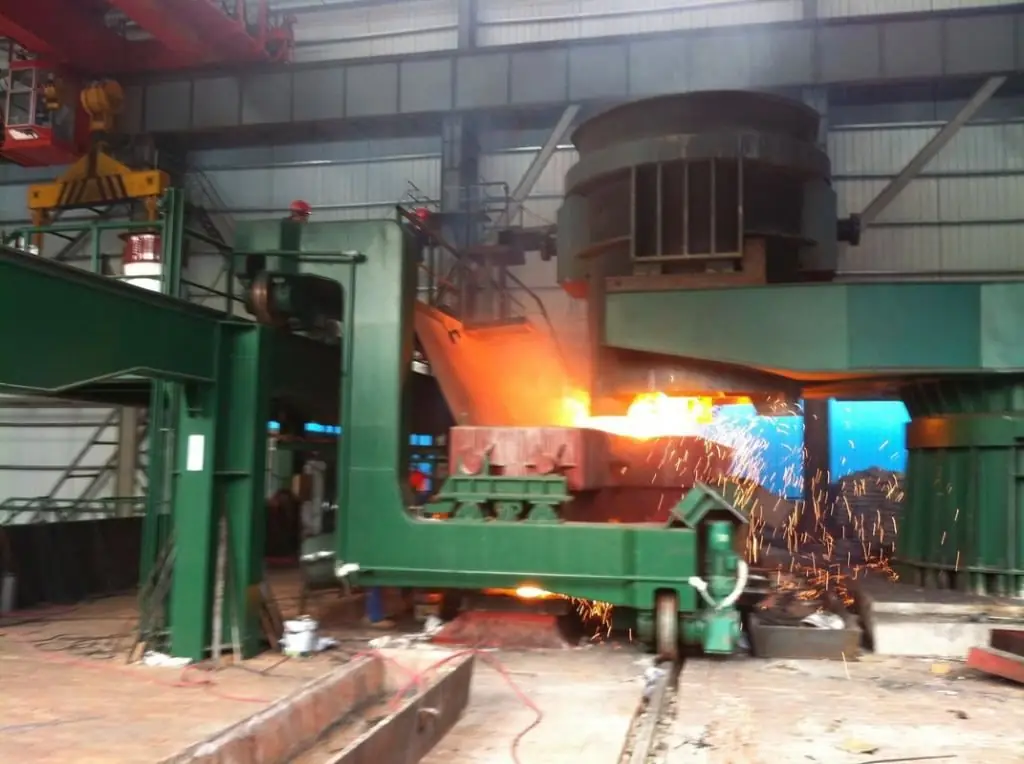
Másodlagos hűtőzóna
Ebben a szakaszban a tuskó legintenzívebb és legközvetlenebb hűtése a permetből érkező víz segítségével történik. Létezik egy speciális rendszer az üresjárati, nem pedig az erőgépes görgőknek. Forgásuk megakadályozza, hogy a tuskó meghajoljon vagy meghajoljon. Ebben a zónában az intenzív hűtés következtében a tuskó falai gyorsan megvastagodnak, és a kristályosodás mélyebbre terjed. A tuskó húzásának sebességét és hűtésének mértékét úgy kell megválasztani, hogy mire a tuskó a húzóhengerekbe kerül, már teljesen szilárd legyen.
Milyen előnyei vannak a folyamatos öntésnek
Mivel ez az acélöntési módszer felváltotta a formába öntést, érdemes ezzel a módszerrel összehasonlítani. Általában érdemes kiemelni a következő előnyöket: nagyobb termelékenység, alacsonyabb költségek és a folyamat munkaintenzitása. A tuskó állandó képződése miatt a zsugorodási üreg a farokba kerül, ellentétben a tuskóformákkal, ahol minden tuskónak saját ürege volt. Emiatt a megfelelő fém kitermelésének százalékos aránya jelentősen megnő. UNRS lehetővé teszi, hogy kapkülönböző formájú munkadarab, a 40x40 mm-es kis négyzettől a 250x1000 mm-es téglalapig. A folyamatos öntőgépek alkalmazása lehetővé tette a forgácsoló malmok teljes elhagyását. Ez jelentősen csökkentette a gyártási folyamat költségeit, és így a piaci árat is. Ezenkívül a kohászati feldolgozás folyamata egyszerűsödött.
Hibák
A folyamat nagyfokú gépesítésének és automatizálásának lehetősége, a jó tuskók nagy százaléka és a fent leírt egyéb előnyök ellenére ennek a módszernek vannak negatív oldalai is. A folyamatos öntéses acél hátrányai a következők.
Először is, nincs lehetőség összetett konfigurációjú ingot előállítására. Másodszor, a bugák és nyersdarabok választéka meglehetősen korlátozott. Meglehetősen nehéz a gépeket úgy átalakítani, hogy más márkájú nyersanyagokat öntsenek, ami megnövelheti egy másik márkájú termék végső költségét, ha azt ugyanabban az üzemben állítják elő. Egyes acélminőségek, például a forrásban lévő acélok, egyáltalán nem készíthetők ezzel a módszerrel.
A folyamatos acélöntési módszer utolsó hátránya nagyon jelentős. Ez egy lehetséges berendezéshiba. Az UNRS kudarca hatalmas teljesítményveszteségekhez vezet. Minél tovább tart a javítás, annál több veszteség nő.
Ajánlott:
Mutatók késleltetés és átrajzolás nélkül: típusok, működési elv, alkalmazás előnyei és hátrányai, szakértői tanácsok
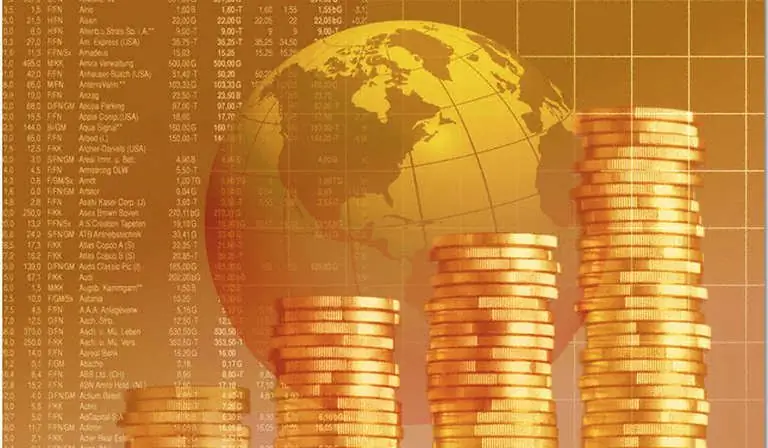
A kereskedésben sokféle eszköz létezik: grafikus konstrukciók, műszaki mutatók, automatizált programok, kereskedési jelek és még sok más. Ahhoz, hogy sikeresen alkalmazhassa őket a kereskedésben, meg kell értenie, hogyan működnek. A késleltetés és az újrarajzolás nélküli indikátorok különösen népszerűek a kereskedők körében
Hoskold-módszer, Ring-módszer, Inwood-módszer – a befektetési tőke visszaszerzésének módjai
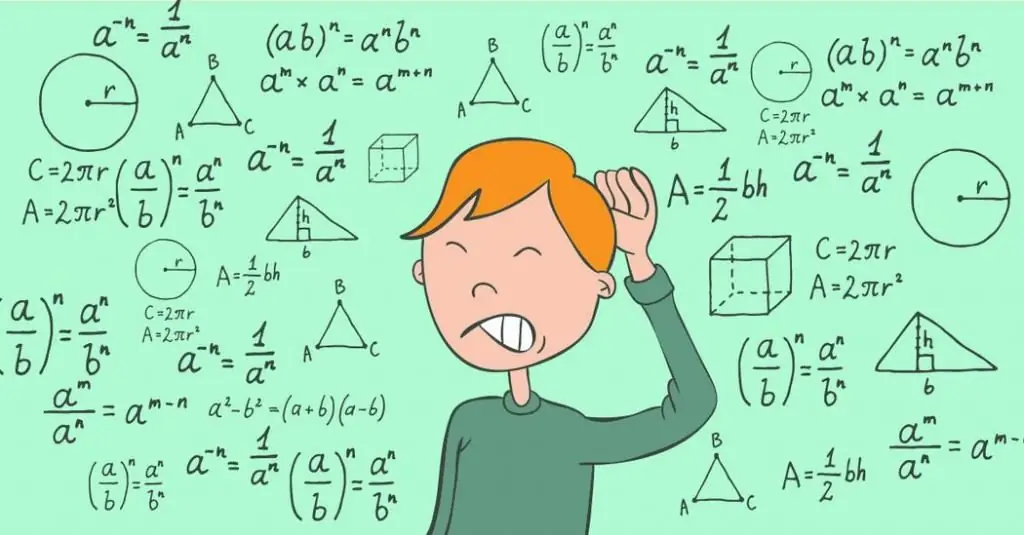
Amikor valaki a saját pénzét fekteti be egy jövedelemtermelő tárgyba, akkor nemcsak nyereséget vár el a befektetett tőkéből, hanem azt is, hogy azt teljes mértékben visszafizesse. Ez történhet viszonteladás útján vagy olyan nyereség megszerzésével, amely nemcsak kamatot hoz, hanem fokozatosan megtéríti a befektetéseket is
A magasnyomás a Magasnyomásos nyomtatási technológia, a fejlesztés korszerű szakaszai, a szükséges felszerelések, az ilyen típusú nyomtatás előnyei és hátrányai
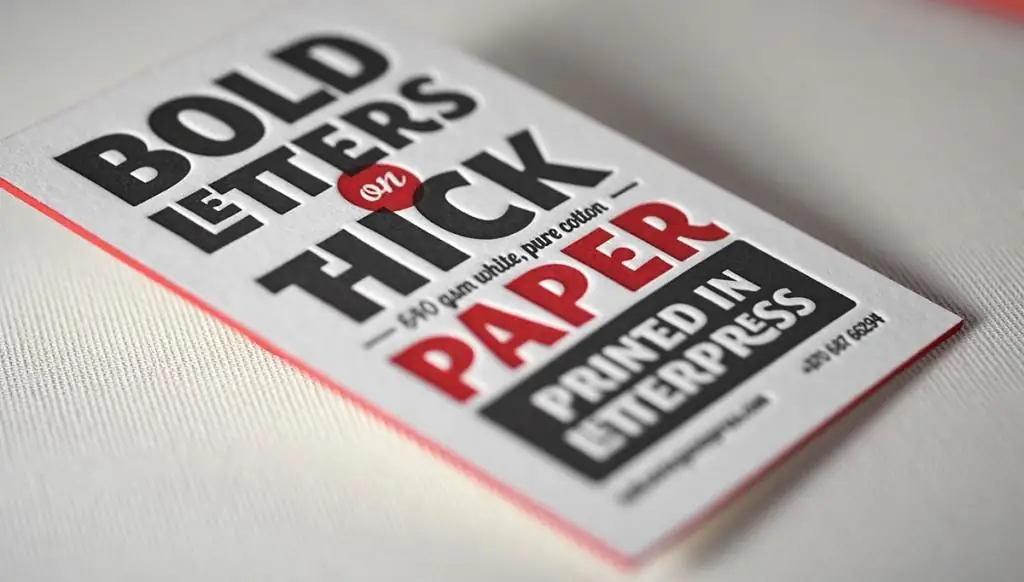
A magasnyomás az egyik tipikus módszer az információ dombormű-mátrix használatával történő alkalmazására. A kiálló elemeket paszta formájú festékkel bevonják, majd a papírhoz nyomják. Így különböző tömeges folyóiratok, segédkönyvek, könyvek és újságok sokszorosulnak
Dízel tengeralattjárók: a keletkezés története, hajóprojektek, működési elv, előnyei, hátrányai és fejlődési szakaszai
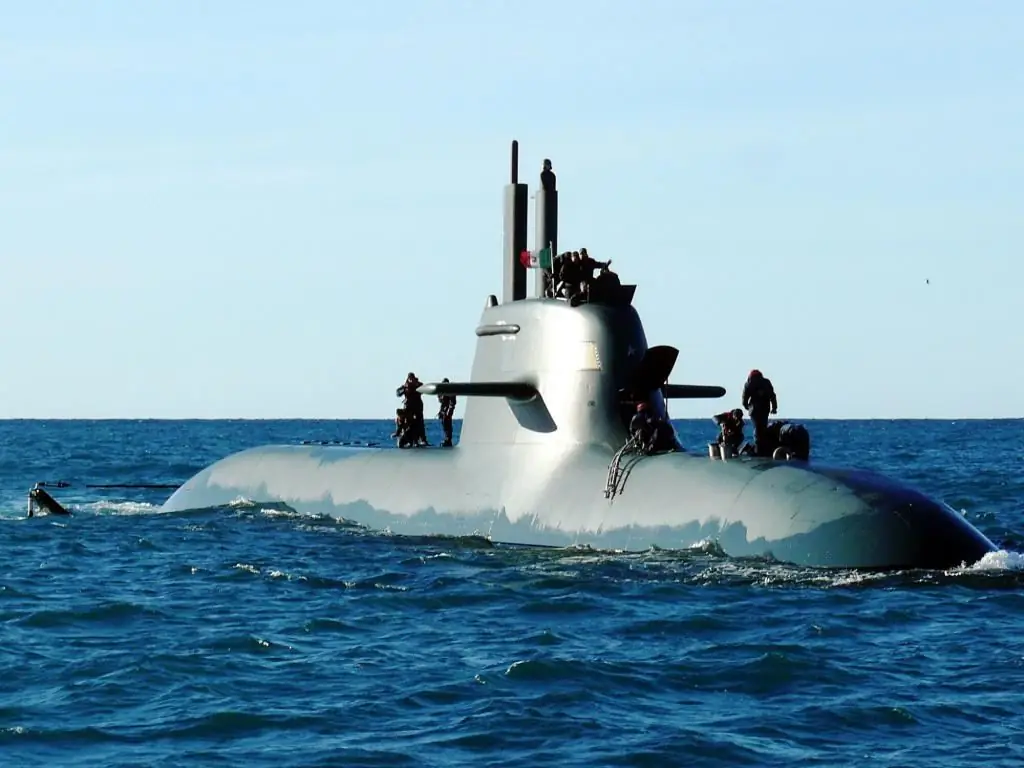
A víz alatt mozgó merülőhajó, tulajdonképpen egy tengeralattjáró prototípusának (a továbbiakban: tengeralattjáró) létrehozásának ötlete jóval a 18. századi tényleges megjelenésük előtt felmerült. Számos legenda nem tartalmaz pontos leírást a víz alatti járművekről, sem a reneszánsz zseni, Leonardo da Vinci
Motor alkoholon: leírás, eszköz, működési elv, előnyei és hátrányai, fotó
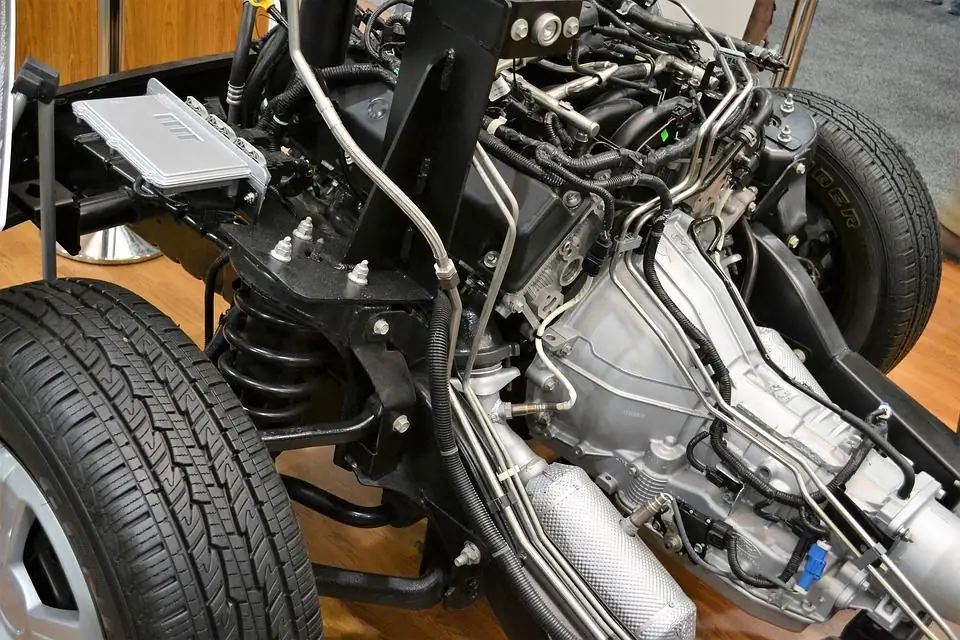
Sok embernek szemrehányást kell tennie az elme tehetetlensége miatt, ami meggátolja őket abban, hogy új lehetőségeket lássanak és a hétköznapi dolgokat alkalmazzák. Például a motor alkohollal. Legyen ne a legjobb megoldás az összes lehetséges közül, de nagyon működőképes. Ezenkívül számos kiviteli alak létezik. Szeszes benzin van. De nem csak őt. Beszéljünk mindent sorban